The construction of a transformer station for a factory involves design, construction, and installation of electrical systems to meet production needs, including steps from survey to regular maintenance.
Preparation and Design of Transformer Stations: Overall Process
The preparation and design stage is the first step in constructing a factory transformer station, involving site surveys, detailed technical designs, and preparation of materials to ensure everything is ready before starting building and installation.
Site Organization and Logistics
In the process of constructing transformer stations, the organization of the site plays a crucial role in optimizing costs and time. Firstly, ensure the construction site is spacious enough for efficient work deployment. Site preparation involves providing adequate electricity and water conditions and arranging labor flexibly according to work volume. Using local materials like sand and stone helps minimize transportation costs.
Transportation of Equipment
The equipment transportation process is divided into two main methods:
- Mechanical: Cables, transformers (TFR), bars, and insulators are important equipment transported by truck to a closed warehouse area at the site.
- Manual: Utility poles and small materials are moved by simple means or manually to ensure safety and cost savings.
Technical Design
The construction of transformer stations must be based on detailed technical designs, including schematic diagrams of main equipment according to grid connection requirements. Detailed drawings help determine dimensions for supports, cable routes, and cable connection methods.
Detailed Drawings
- Support dimensions: Important for determining elevation, location of transformer installation, and auxiliary equipment.
- Cable route: Shows the route, elevation, ensuring accuracy in equipment connections.
- Installation accessories: Details about types of bolts, brackets, and assembly diagrams are extremely necessary.
Equipment Preparation
Before installation, thorough inspections through catalogs and materials are necessary. Ensure that the equipment’s technical specifications, such as rated voltage and current, match the placed order.
Construction Process
- Excavate holes, bury foundations: Creating foundations for electric poles and transformer support is the first important step.
- Install steel frames: Use jacks to place the transformer on the steel frame safely and stably.
- System connection: Ensure accurate electrical cable connections, distribution cabinet installations, and measurement devices.
Labor Safety
In the construction process of transformer stations, labor safety is always prioritized. Staff must comply with PPE regulations and check grounding, insulation systems of transformers before operation.
Required Documents
Necessary documents include legal records like connection request forms and approved schematic diagrams. Additionally, the installation manual from the manufacturer is an important information source.
Technical standards TCVN and IEC for medium voltage electricity must be strictly followed to ensure overall quality and safety of the transformer station.

Building Infrastructure for Transformer Stations
The infrastructure construction process includes excavating foundations, installing grounding systems, and pouring concrete foundations to create a solid foundation, as well as installing underground protective conduits for the safe electrical system.
Building infrastructure for the transformer stations involves a detailed and thorough process to ensure electrical safety and operational efficiency. It starts with surveying and identifying the location, where factors like pole foundation and medium voltage underground cables are carefully selected to avoid impacting roads and residential areas. Site preparation tasks include excavating holes, building foundations, provided sufficient electricity and water for construction, and ensuring effective transportation of materials and equipment to the site.
One crucial step in this process is installing the grounding system, which determines the electrical safety of the entire project. This system is implemented by creating grounding electrodes spreading the lightning current, helping to avoid lightning strike risks.
Then, pouring the transformer station concrete foundation helps create a stable base for the transformer, ensuring stability during the operation process. Electrical devices such as circuit breakers, operation stools, bars, insulators will be erected to ensure efficiency in controlling the electrical flow. The installation process of the transformer requires precision when using a crane to place the transformer in the correct position.
Installing medium voltage underground cables is also an indispensable part, playing a role in connecting the transformer station to the power source, safely and efficiently transmitting electricity. Connecting the transformer station to the existing electrical system must be done carefully to ensure a safe connection.
Finally, the process of testing, adjustment, acceptance, and trial run is conducted to check the entire system, ensuring everything works smoothly before handing over to the customer.
The factor of labor safety is always a top priority along with the standard of quality equipment and compliance with technical regulations throughout this process.
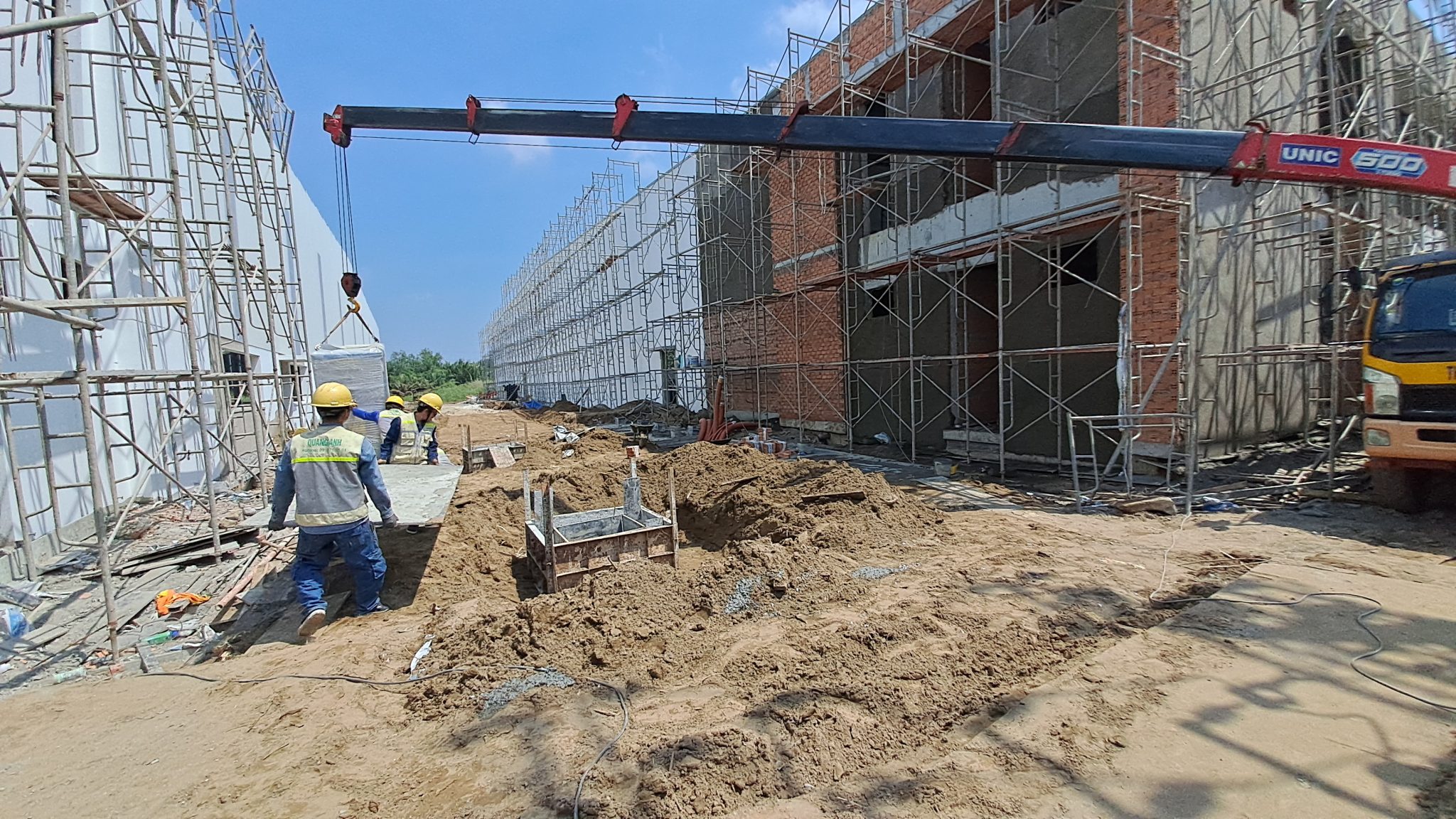
Installing Equipment for Transformer Stations
The equipment installation phase includes erecting circuit breakers, operation stools, and placing transformers in positions using cranes to ensure electrical safety and effective operation of the system.
- Site preparation and documentation: Thorough field surveys to determine optimal positions for transformer station foundations, underground cable routes, and the grounding system. Ensure the completion of all necessary legal procedures, including installation registration records and schematic diagrams. The site must be organized tightly, from electricity and water supply to labor arrangement.
- Foundation and auxiliary system construction: Conduct excavating and installing protective tubes with precise positions according to approved designs. The grounding system must be constructed following electrical safety standards, then pour concrete foundations with standard materials to secure the equipment.
- Installing main equipment and accessories: The transformer must be moved and placed on the prepared foundation, noting to check balance and mechanical connections. Install cutting devices such as circuit breakers, operational stools, supportive bars with insulator accessories. Medium voltage cables are routed through underground conduits, making sure they are not twisted or damaged in insulation.
- Connection and trial operation: Electrically connect the transformer to the grid system and auxiliary devices. Place warning signs and station nameplates according to safety regulations. Conduct tests and calibrations on operational parameters such as grounding resistance and idle current.
- Acceptance and handover: Final check to ensure everything is executed correctly, cable trenches covered and cleaned. Measure environmental parameters such as temperature and humidity within allowable limits. Electricity is switched on, and no-load running is done before handing over to the management unit.
Technical notes:
- Strictly comply with electrical safety and lightning protection standards.
- Use certified quality materials such as cables from reputable brands: Cadivi, LS, Eaton, Schneider.
- Conduct regular maintenance work, including checking grounding systems and transformer oil to maintain stable operations.
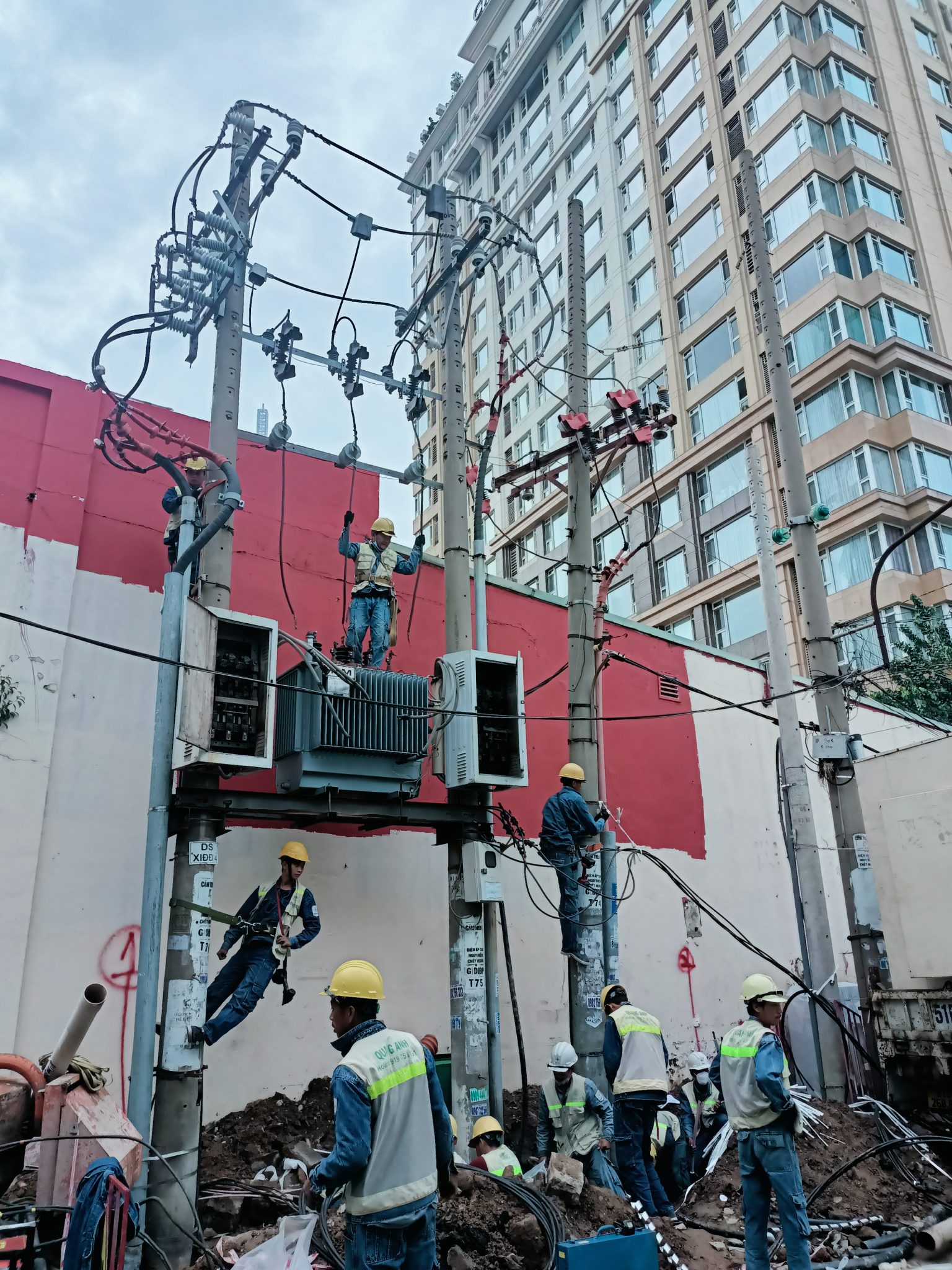
Connecting and Testing the Electrical System
After installing the equipment, the process of laying out medium voltage cables and connecting the transformer station takes place, followed by testing, calibrating, and accepting to ensure the system operates accurately and safely before operation.
In the electrical system engineering field, testing electricity is a vital step to ensuring performance, safety, and the lifespan of equipment before being put into use. This process checks aspects such as insulation, load capacity, and system operational efficiency.
- Insulation resistance test: Measure the insulation capability of the equipment to detect the potential for current leakage, ensuring system safety.
- Partial Discharge (PD) Testing: Aims to detect partial discharges in insulation cores, protecting the equipment from unexpected losses.
- Hi-Pot Test: Tests the equipment’s ability to withstand high voltage to ensure safety and prevent the risk of fire and electric shock.
- Ratio tests: Conducted on transformers and current transformers to determine equipment accuracy, contributing to grid stability.
- Ground resistance measurement: Assess the effectiveness of the grounding system, an important part of lightning protection and electrical stability.
System connection process
The connection and testing process of the electrical system is performed according to Decision 25/QĐ-ĐTĐL (2019). The main steps include:
- AGC (Automatic Generation Control) connection: Verify the local and remote control status through the SCADA/EMS system to ensure consistency in operations and quickly detect incidents.
- FRS connection: Ensure compatibility and reliability of the load dispatching system as well as record in the regulated form, ensuring a professional and accurate acceptance process.
Applicable devices
The testing process applies to devices such as:
- Transformer/CT/PT: Check core characteristics and coil resistance to ensure the equipment operates per design requirements.
- Capacitor bank: Measure current, reactive power, and check connection points, optimizing performance and reducing electricity losses.
- Grounding system: Evaluate mechanical durability and earth resistance to ensure safety for the electrical system.
Purpose and standards
The testing process not only ensures operational safety, minimizes fire risk but must also comply with legal standards like IEC 62271 and TCVN 3715. These standards provide a solid foundation to optimize performance and ensure load balancing and grid stability.
Legal reference documents
Reference documents include important standards and decisions such as Decision 25/QĐ-ĐTĐL (2019), IEC 62271, and TCVN 3715, guiding testing activities and ensuring this process follows the law.
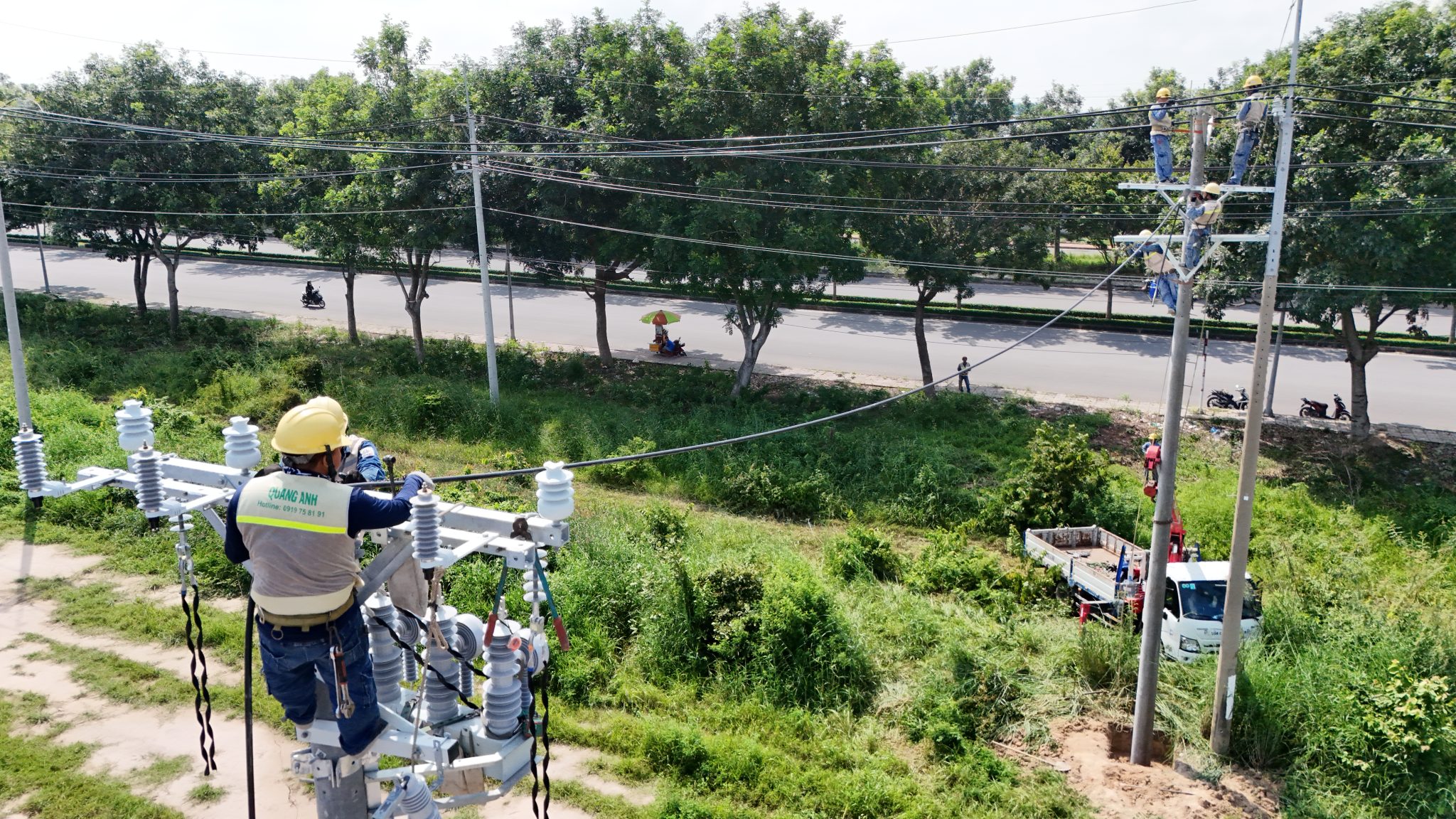
Notes and Equipment Safety for Transformer Stations
Finally, installing nameplates and warning signs to clearly inform the position and danger of the transformer station combined with regular maintenance ensures long-term safety and stable operation.
Transformer stations play a crucial role in the power system, transforming voltages to distribute electricity to different regions. To ensure transformer station safety during operation and maintenance, complying with specific measures is absolutely necessary.
Notes
The notes related to the transformer stations include important contents such as:
- Maintenance history: This record monitors all maintenance and inspection activities of the system to maintain equipment performance.
- Operational procedures: Details steps to be taken before, during, and after operations, thereby optimizing operational efficiency.
- Incident reports: Document any incidents that occur, along with timely remedial solutions.
Safety Equipment
In transformer stations, safety is paramount, with the role of electrical protective equipment and workplace environmental protection as follows:
- Safety Equipment for Personnel:
- Protective clothing: Such as reflective vests, safety boots, and specialized goggles.
- Protective equipment: Use rubber gloves, gas masks to prevent potential hazards.
- Electrical Equipment:
- General circuit breakers: This equipment must always be ready to cut the entire power in necessary cases.
- Electrical network diagram: Providing detailed diagrams helps easier tracking and control.
- Protective equipment: Transformers and current transformers must be properly grounded to prevent electrical fires and explosions.
- Protection of the Working Environment:
- Electrical fire prevention: Place fire extinguishers in accessible positions, combined with automatic fire alarm systems.
- Ventilation: Especially in rooms containing devices like batteries, maintaining ventilation to avoid gas poisoning is necessary.
- Technical Regulations:
- Compliance with regulations: Follow regulations such as Circular 38/2019/TT-BCT to meet the highest safety standards.
For Temporary Electric Works
- Electrical cabinet arrangement: Should be placed in a dry place or high up to avoid moisture.
- Full grounding: Ensure grounding to minimize the risk of electric shock.
Working with Battery Systems
- Wear protective clothing: Use specialized clothing and gloves when exposed to acids and alkalis.
- No fire and smoking: Stay away from battery storage areas to prevent fire hazards.
- Ventilation: The battery room must have a ventilation system to prevent toxic gas accumulation.
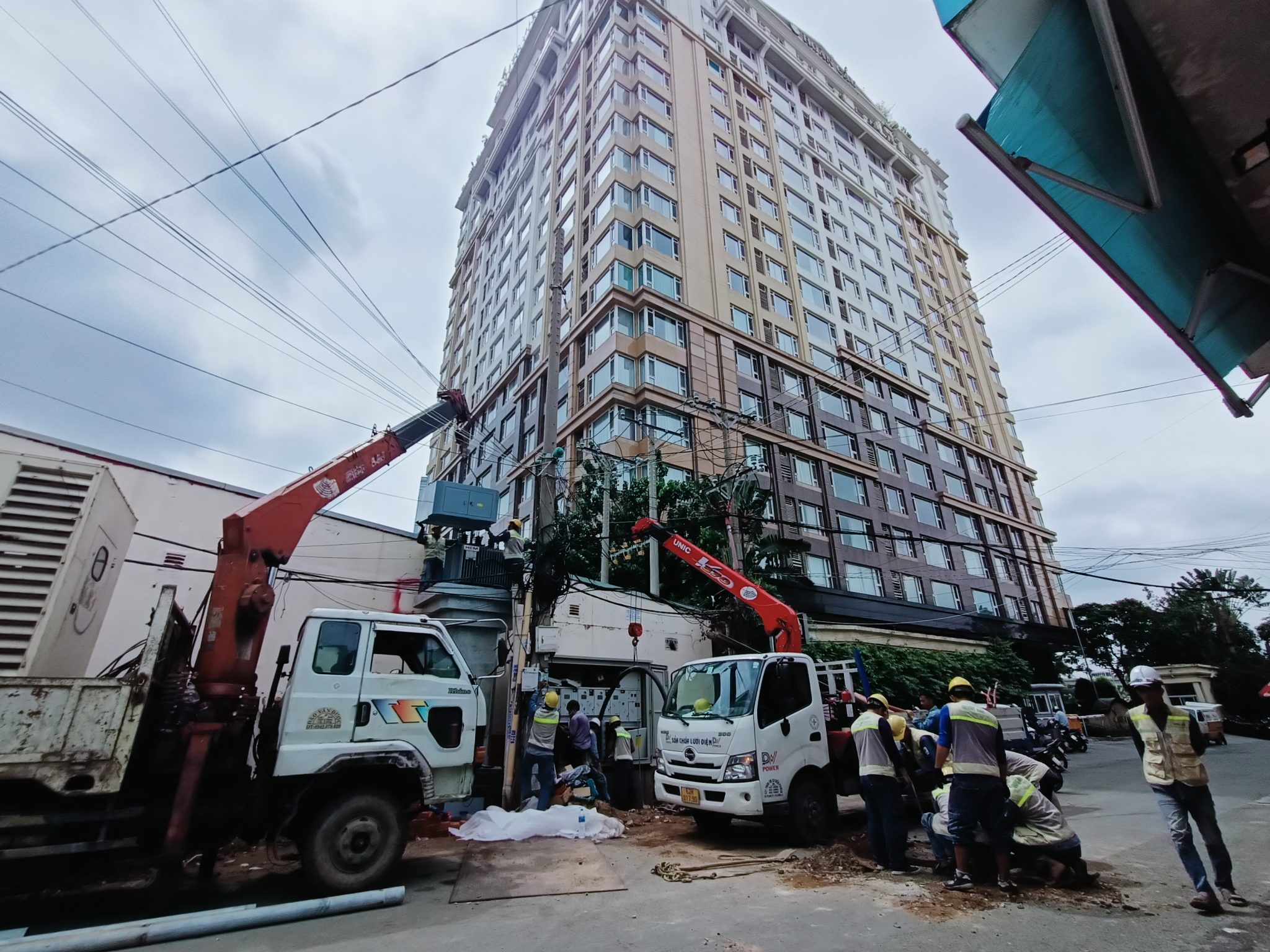
Factory transformer station construction ensures stable and safe energy provision for production activities, offering superior technical benefits and optimizing long-term investment.
For factory transformer station construction projects, contact QuangAnhcons via phone at +84 9 1975 8191 for detailed consultation.
QuangAnhcons provides professional factory transformer station construction services, including from technical design to installation and periodic maintenance, ensuring effectiveness and safety for clients.