Upgrading factory power systems is a complex process that involves assessing, designing, and executing installations to meet new power demands and improve operational efficiency.
Factory Power System Upgrade Process
The factory power system upgrade process includes practical steps such as assessing the current condition and evaluating power consumption needs; designing a new system based on Vietnam standards (TCVN); executing cable installations with appropriate materials and technology choices like main power supply cables, cable trays, and installing electrical equipment such as MSB distribution cabinets and grounding systems. Finally, conduct trial operations and hand over regular maintenance to ensure stable system operation.
Assessment and Status Evaluation
- Analyze the old electrical system: The first step in the factory power system upgrade process is to analyze the capacity, condition of conductors, switchgear, and the system’s current demand response capability. This will help clearly identify elements that need to be changed or upgraded to meet current electrical system standards.
- Determine power load needs: Calculating current consumption is essential for forecasting growth and selecting suitable equipment.
- Risk detection: Evaluate safety weaknesses and overload risks to propose remedial measures.
Redesign the System
- Prepare technical drawings: Adjust the placement of electrical cabinets, wiring, and lighting equipment according to TCVN standards.
- Select materials and equipment:
- Dynamic cables: Choose cable cross-sections based on load capacity, voltage drop, and cable laying method (underground/overhead).
- Protective equipment: Use MCCB/ACB with an appropriate cut-off current to protect the standard electrical system.
- Cable Schedule Board: List detailed cable specifications for efficient construction management.
Prepare Materials and Equipment
- Procurement of materials: Priority should be given to energy-saving devices with quality certification.
- Quality control: Ensure that all devices meet IEC or TCVN standards before installation, optimizing power usage.
Execution of Upgrades
- Install medium-voltage underground cables: Use uPVC or HDPE pipes and connect cables from the source to the substation with specialized terminals.
- Replace distribution cabinets: Integrate metering systems and install dry transformers to reduce energy losses.
- Lighting system: Arrange lights to ensure standard illumination and use smart switches for automation.
Testing and Acceptance
- Dry run testing: Ensure each electrical circuit can operate safely.
- Safety factor measurement: Insulation resistance must be ≥ 1 MΩ, and voltage drop must not exceed 5% according to TCVN standards.
- Hand over documents: Provide electrical diagrams and operation manuals for long-term power system maintenance.
Optimization Post-Upgrade
- Energy monitoring: Install a SCADA system to manage real-time power consumption.
- Regular maintenance: Perform electrical cabinet cleaning, terminal tightening, and timely replacement of aged equipment.
Applicable Standards
- Electrical safety: Adhere to QCVN 12:2015/BCT regarding electrical equipment installation.
- Energy-saving: Apply the DSM model to manage power consumption.
Important Notes
- Coordination with EVN: Permission must be obtained from the power distribution unit prior to medium-voltage system connection.
- Staff training: Provide training for technicians to ensure they can effectively operate the new system.
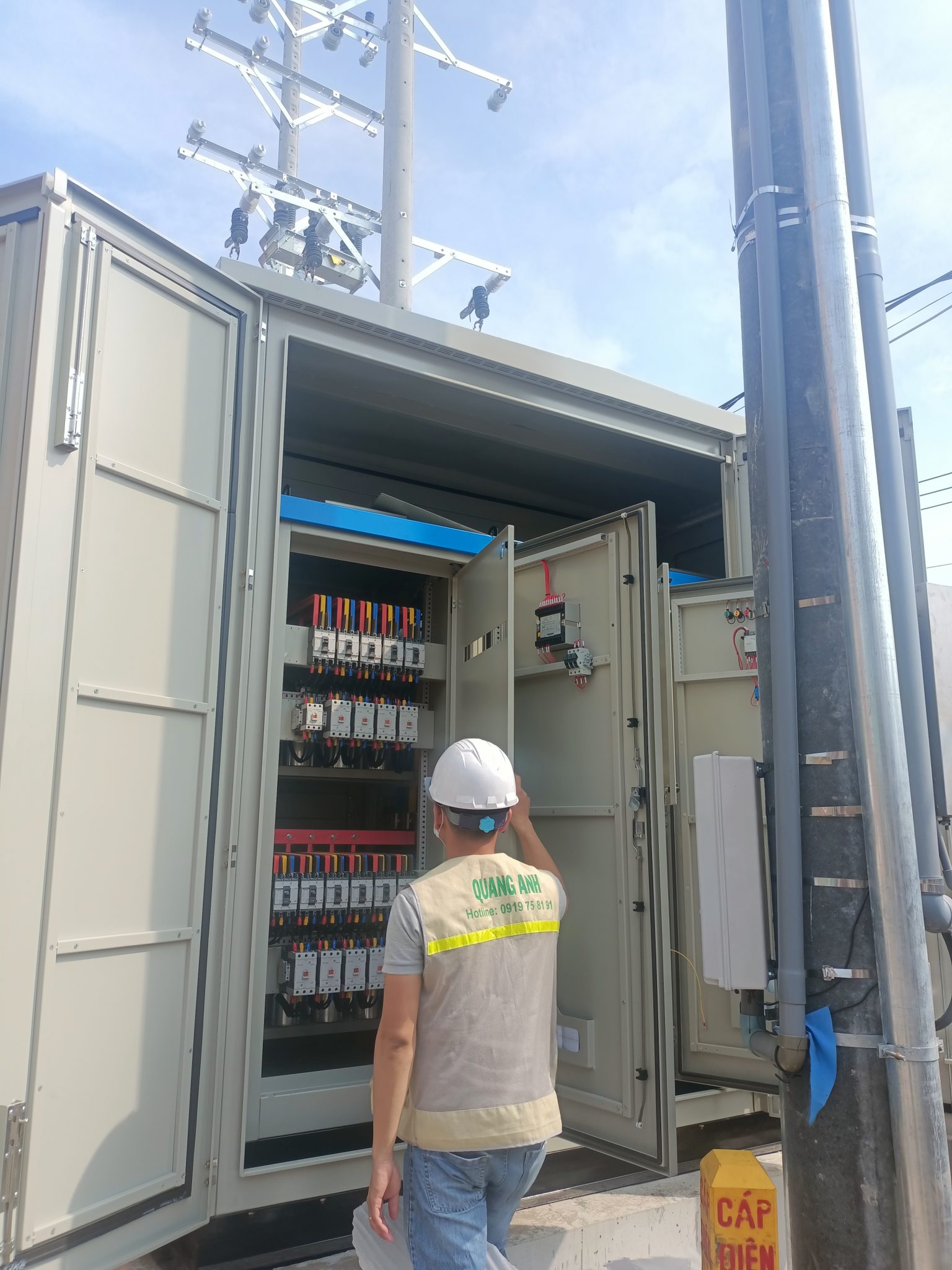
Technical Factors in Factory Power System Upgrade
Important technical factors in upgrading factory power systems include labor safety with personal protective equipment, cost optimization through the selection of durable materials and smart power adjustment systems, and adherence to legal standards such as TCVN 9206:2012 to ensure quality and safety in industrial electrical installations.
When upgrading factory power systems, calculating the total power consumption is necessary to select suitable conductors and ensure stable system operation. This is a preliminary and crucial step to prevent overload, directly affecting equipment and labor safety.
Another factor is designing the main power source cable system. Depending on the actual conditions of the factory, cables may be laid openly or installed underground through PVC or metal pipes to ensure efficiency and ease of maintenance.
Electrical cabinet layout is an essential part. Electrical cabinets such as distribution boxes, central control cabinets, ATS panels, and capacitor banks need to be arranged logically to optimize space and facilitate easy handling when needed, preventing the spread of incidents.
The light electrical system must also be focused on, ensuring sufficient lighting, stable network connections, and reliable fire alarm systems. This process must strictly adhere to industrial electrical standards to enhance stability and safety.
Safety and efficiency in upgrading factory power systems are top priorities. The system should be designed to minimize power wastage, ensuring the safety of workers and equipment throughout the operation.
Finally, designing the lighting system must carefully consider the number of lights to avoid disrupting production and not waste electricity.
After installation completion, acceptance and testing of the system are essential steps to ensure everything operates efficiently before officially putting it to use.
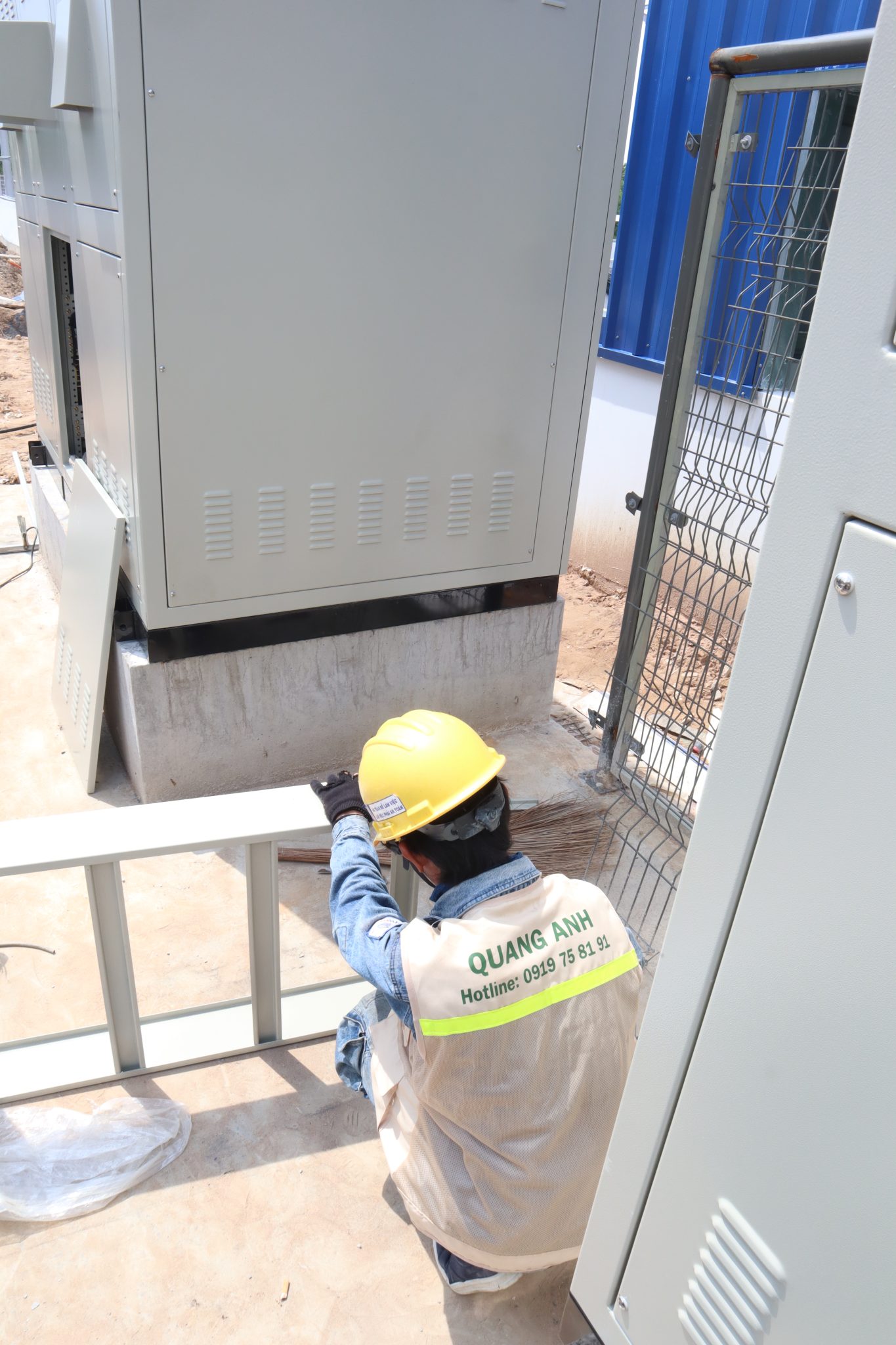
New Technology Trends in Factory Power Systems
New technology trends in upgrading factory power systems include IoT monitoring systems integrated with measuring sensors for early fault warnings, integrating rooftop solar panels to operate from renewable energy sources, and applying PLC for automated power distribution, optimizing operations and reducing costs.
The year 2025 is a time of significant change in the factory power system industry, where new technologies are being applied to improve performance and reduce costs. One standout trend is solar power technology, where the use of high-efficiency solar panels with hybrid perovskite and improved silicon materials can achieve energy conversion efficiency of over 30%. This not only enhances economic efficiency but is also environmentally friendly.
Factories can take advantage of installing large rooftop solar power systems to reduce dependence on the grid and energy costs. The integration of AI in power systems is another important step forward, allowing for data analysis for weather and consumption demand prediction, thereby optimizing operating capacity.
Energy Optimization and Factory Power Saving
Power system optimization involves conducting energy audits to identify and reduce waste. Additionally, adjusting device operation schedules to exploit off-peak hours contributes to an effective factory power-saving strategy. Old equipment should be replaced with high-efficiency devices, optimizing energy and saving costs.
Moreover, training employees in energy-saving awareness is essential, alongside regular electrical system maintenance to ensure operational efficiency and limit incidents.
Enhanced Electrical Network System
To enhance transmission and distribution capacity, the electrical industry is investing in new technology to improve power grid infrastructure. These advancements not only increase system efficiency but strongly support sustainable development goals by promoting the use of renewable energy.
In a rapidly changing landscape, advanced technologies like solar power and artificial intelligence are playing crucial roles in revolutionizing factory power systems. Focusing on investment and applying these solutions will help businesses not only reduce costs but also contribute to environmental protection.

The process of upgrading factory power systems offers numerous benefits not only in terms of technical and investment strategies but also helps improve performance and reduce long-term costs.
Contact QuangAnhcons now via Hotline: +84 9 1975 8191 for professional factory power system upgrade consultation.
QuangAnhcons provides factory power system upgrade services from design, implementation to maintenance with a team of experienced engineers and advanced technology.