Installation of industrial electrical systems is an essential part of factories and production facilities, encompassing everything from design, and construction to safe and efficient system operation.
Industrial Electrical System Installation Process
Industrial electrical system installation begins with design and planning, including determining power requirements and layout of industrial electrical cabinets. Next, main power cable construction from the substation to the main switchboard using underground cables. Cable trays play a critical role in securing wires, requiring stability and alignment. Industrial electrical cabinets are a distribution center that requires both high technical and aesthetic standards. Light electrical systems such as factory lighting and fire alarms must always ensure safety and convenience.
- Preparation and Survey
- Preparation of equipment is the foundation of the industrial electrical system installation process. This includes transformers, electrical conductors, switchboards, system protective devices, and other equipment such as signal lights. A good preparation plan helps optimize time and cost.
- Site surveys play an important role in clearly determining specific technical requirements and the installation locations of key equipment such as substations and generators.
- System Design
- Designing electrical system drawings for industrial use requires compliance with technical standards and meeting specific business requirements. The goal is to optimize space and functional efficiency of the system, ensuring that the location and size of equipment like substations, and generators are appropriate.
- Choosing the right equipment ensures efficient system operation and meets the power demands of the facility. Brands like ABB, Mitsubishi, Cadivi may be considered to ensure quality.
- Main Power Cable System Construction
- Installing the main power cable system is a crucial step, commonly executed from the substation to the main switchboard (MSB) using underground or overhead cables, depending on the project design.
- Calculating the necessary capacity for the cable system ensures load bearing and safe operation throughout the facility.
- Cable Tray Construction
- Cable tray construction not only protects and secures electrical cables but also creates a tidy and professional aesthetic for the system.
- The cable installation process must be conducted quickly to avoid disruption and ensure system safety.
- Completion and Inspection
- Complete system installation following the approved design blueprint, ensuring all equipment and connections are implemented accurately.
- A thorough inspection of the entire system ensures stable and safe operation, including all protection and monitoring systems.
Safety Standards
- Throughout the installation process, adherence to technical and safety standards is crucial to ensure that the industrial electrical system can operate sustainably and safely.
- Ensure all personnel involved in the installation are well-equipped with knowledge and trained in both technical and labor safety.
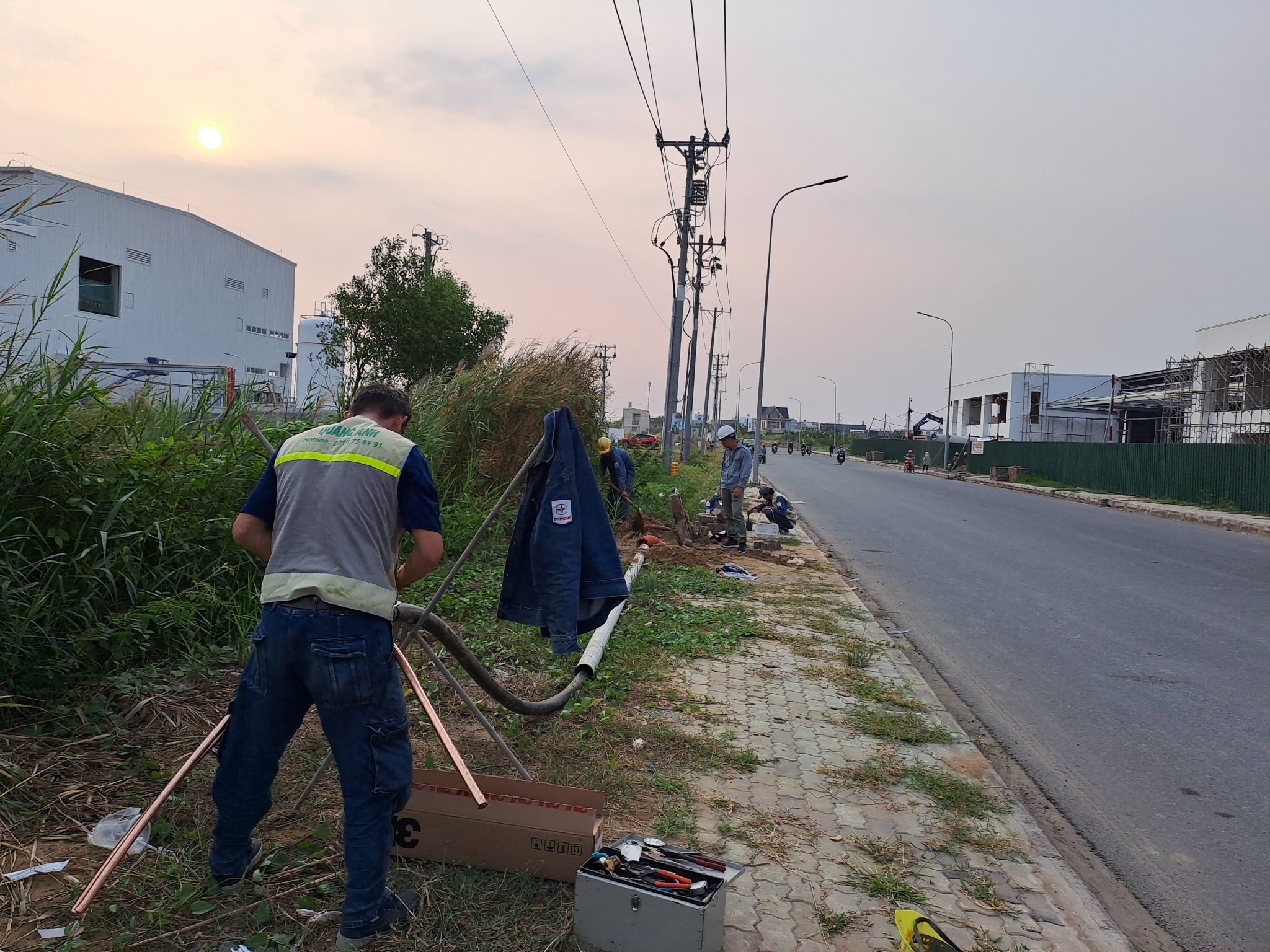
Safety notes when installing industrial electrical systems
Safety is the top priority in installing industrial electrical systems. The use of power cables and cable trays must not pose any danger to personnel and equipment. The focus is on efficiency and optimization to reduce energy waste. Industrial electrical standards must be complied with to ensure everything operates stably and reliably.
In the process of installing industrial electrical systems, ensuring the safety of the electrical system is of utmost importance. Below are the key notes to help managers and engineers effectively achieve this.
System Design and Planning
- Electrical load calculation: Base the electrical load calculation on determining the electricity needs of each area in the facility. This helps design electrical circuits to handle the necessary power without overloading.
- Reasonable layout: Structure the areas using electricity in a reasonable manner to ensure easy management and repair in the event of a problem.
Compliance with Safety Standards
- Ensure electrical safety: Strictly adhere to the state’s industrial electrical standards to minimize the risk of electrical accidents, thus creating a safe working environment for employees.
- Use protective devices: Installation of protective devices such as shock protection and overload prevention systems is necessary to prevent potential issues during operation.
Thorough Installation and Inspection
- Proper technical execution: The installation process must follow the correct procedures and techniques to achieve maximum stability and efficiency.
- Pre-operational inspection: Conduct thorough acceptance and inspection of the system before use to ensure all devices and systems operate correctly and safely.
Maintenance and Optimization
- Regular maintenance: Performing regular maintenance of the electrical system helps early detection and timely resolution of potential issues, keeping the system in optimal working condition.
- Optimize energy use: An efficiently designed and operated electrical system is one that can optimize energy consumption, avoid waste, and help reduce energy costs.
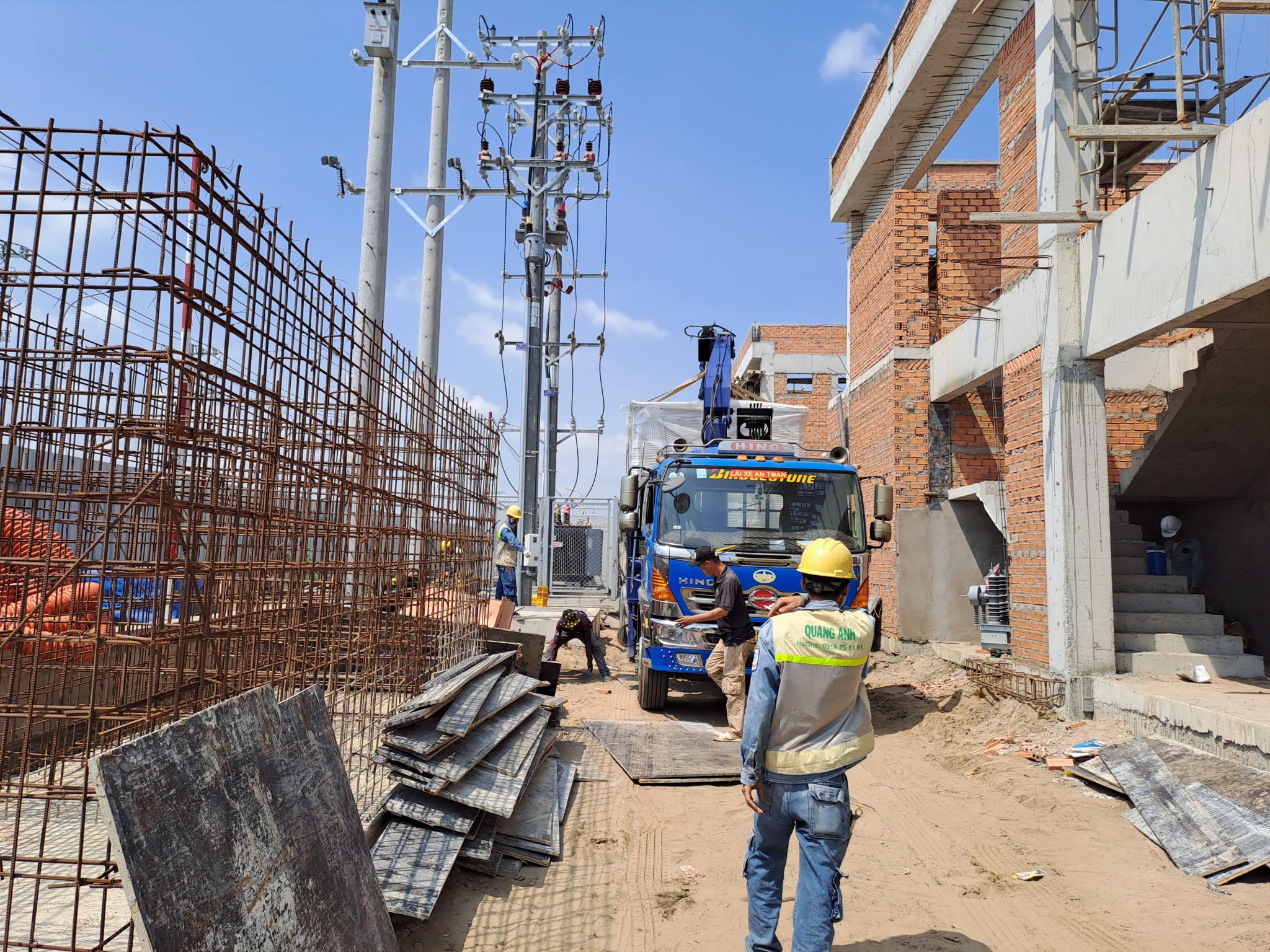
Inspection and acceptance of industrial electrical systems
Once installation is complete, system testing and trial runs must be conducted to ensure operation according to design. The final acceptance and handover procedures confirm that everything from industrial switchboards to factory lighting works efficiently and meets standards.
During the development and completion of industrial electrical systems, inspection and acceptance play a core role in confirming that all components operate according to design and meet the highest technical standards.
Acceptance Process
This process includes three main stages, conducted sequentially to ensure continuity and effectiveness.
- Cold Acceptance:
- Initially, inspect and confirm the quality of electrical materials and equipment. Legal records such as equipment history and factory inspection certificates must be fully verified to ensure equipment readiness for grid connection.
- Power-On Acceptance:
- Next, perform a comprehensive inspection of the electrical system to ensure technical parameters are met accordingly. The operational capabilities and protective systems must be thoroughly evaluated to avoid potential risks.
- Handover Acceptance:
- Finally, the system is handed over after successful inspection and trial operation, ensuring readiness for official use.
Acceptance Standards
To achieve optimal status for industrial electrical systems, the following standards must be ensured:
- Safety: The safe distance between live parts and the ground, along with grounding values, must meet the highest safety standards to ensure safety for personnel and equipment.
- Performance: The power supply capability must be strong enough to meet the operational needs of all equipment in the facility.
- Standards Compliance: The entire system must comply with current light electrical and technical regulations, thereby optimizing operational capabilities.
Inspection Procedures
The role of inspection is critical in the acceptance process.
- Device Inspection: All devices must be checked to ensure they function as designed.
- System Inspection: Conduct trial runs of the entire system to confirm stability and safety.
Warranty and Maintenance
After the industrial electrical system is accepted, the warranty and maintenance phase begins with the goal of maintaining stable operational efficiency for the entire system in the long term.
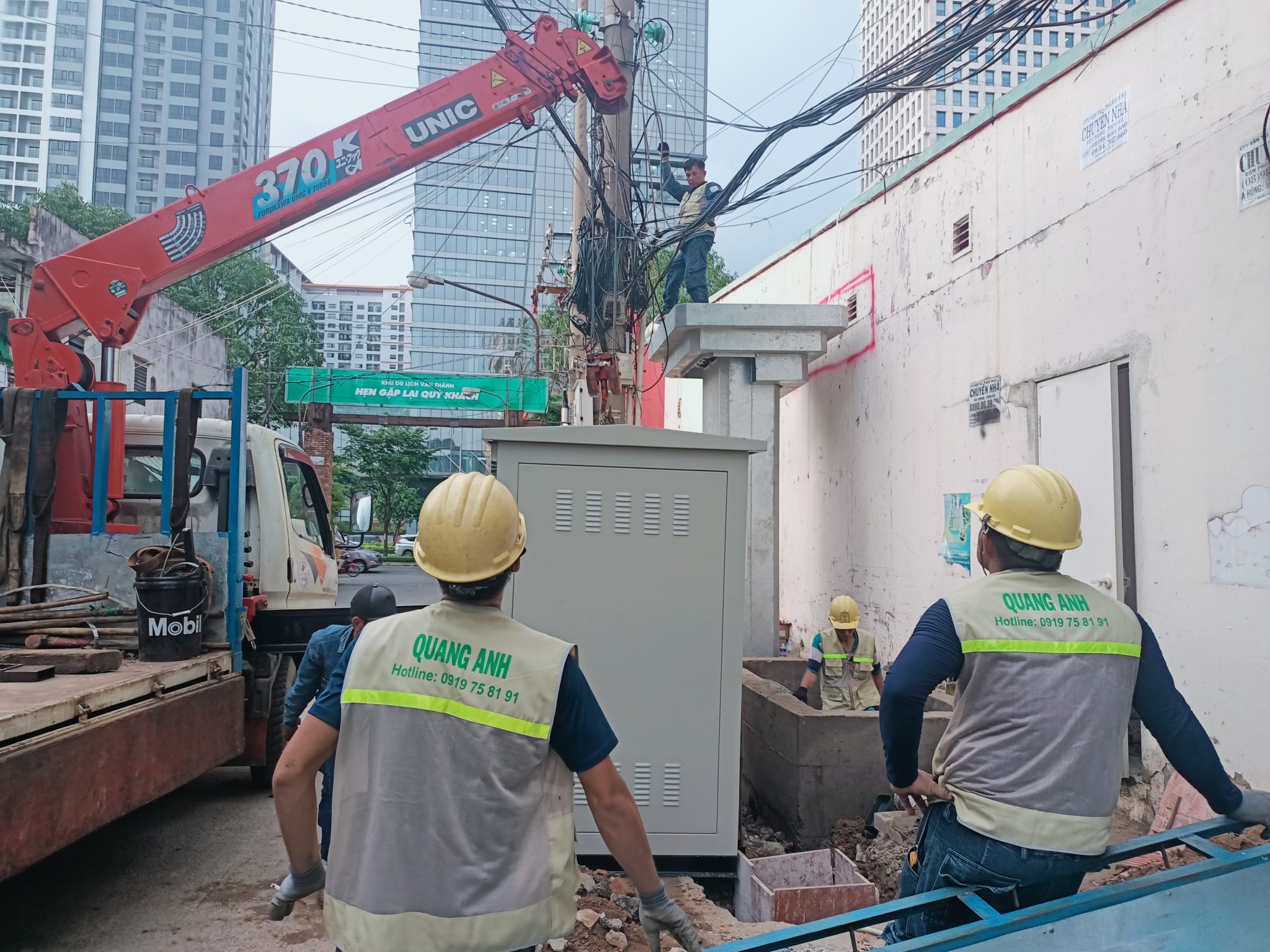
The installation of industrial electrical systems not only ensures safety but also optimizes performance for production activities, contributing to the technical and strategic success of the business.
Contact QuangAnhcons now for safe and efficient industrial electrical system installation. Call Hotline: +84 9 1975 8191 for detailed consultation.
QuangAnhcons specializes in providing industrial electrical system installation services with professional processes, ensuring compliance with industrial technical standards, delivering safety and superior performance for production facilities.