Industrial Electrical Systems are critical in production operations, comprising 40-60% of factory M&E volumes. The process and technical requirements play a key role.
5-Step Process for Industrial Electrical System Design
The industrial electrical system design process begins with receiving information and conducting actual surveys. Engineers must gather data on area, machinery, manufacturing industries, and corporate electricity needs. This foundational step helps determine total power consumption, guiding equipment selection. Next, designing the high-voltage network with the layout of lines, substations, and power cabinets is necessary to conduct electricity from the national grid to the factory. For the low-voltage network, it is critical to ensure the voltage is below 1kV and that the lighting system is carefully calculated to meet the needs of each area, avoiding waste or insufficient lighting.
- Receive customer information: The industrial electrical system design process begins with engineers receiving and surveying practical information from customers. To ensure accurate electricity network design, it is crucial to collect detailed data such as floor area, number of employees, type of machinery in use, and basic factory characteristics.
- Consultation and proposals: After gathering sufficient information, engineers will advise customers on feasible, safe, and cost-effective design options. Selecting equipment and materials must be careful, ensuring they suit the actual conditions and meet project requirements.
- Draft design drawings: Based on the information and selected options, industrial electrical drawings are created to show the layout of equipment, lines, along with operational areas. This process is particularly helpful in providing customers with an overview of the electrical system before moving to the next stage.
- Submit preliminary design for customer approval: A crucial step in the industrial electrical system design process is obtaining customer approval on the preliminary drawings. This close interaction ensures that all requirements are met, from features to safety and aesthetics.
- Finalize the design: After receiving customer feedback, the design will be refined and completed, ready for construction. This phase is decisive for the safety and efficiency of the subsequent industrial electrical system.
Key Factors in Design
- Load calculation: An indispensable process to determine the maximum electrical consumption, ensuring sufficient energy for all production activities.
- Design of high-voltage and low-voltage networks: The procedures must be precisely executed to ensure safety and efficiency once the system is operational.
- Material and equipment selection: Using insulating materials and safety equipment like circuit breakers to protect the system from unwanted incidents.
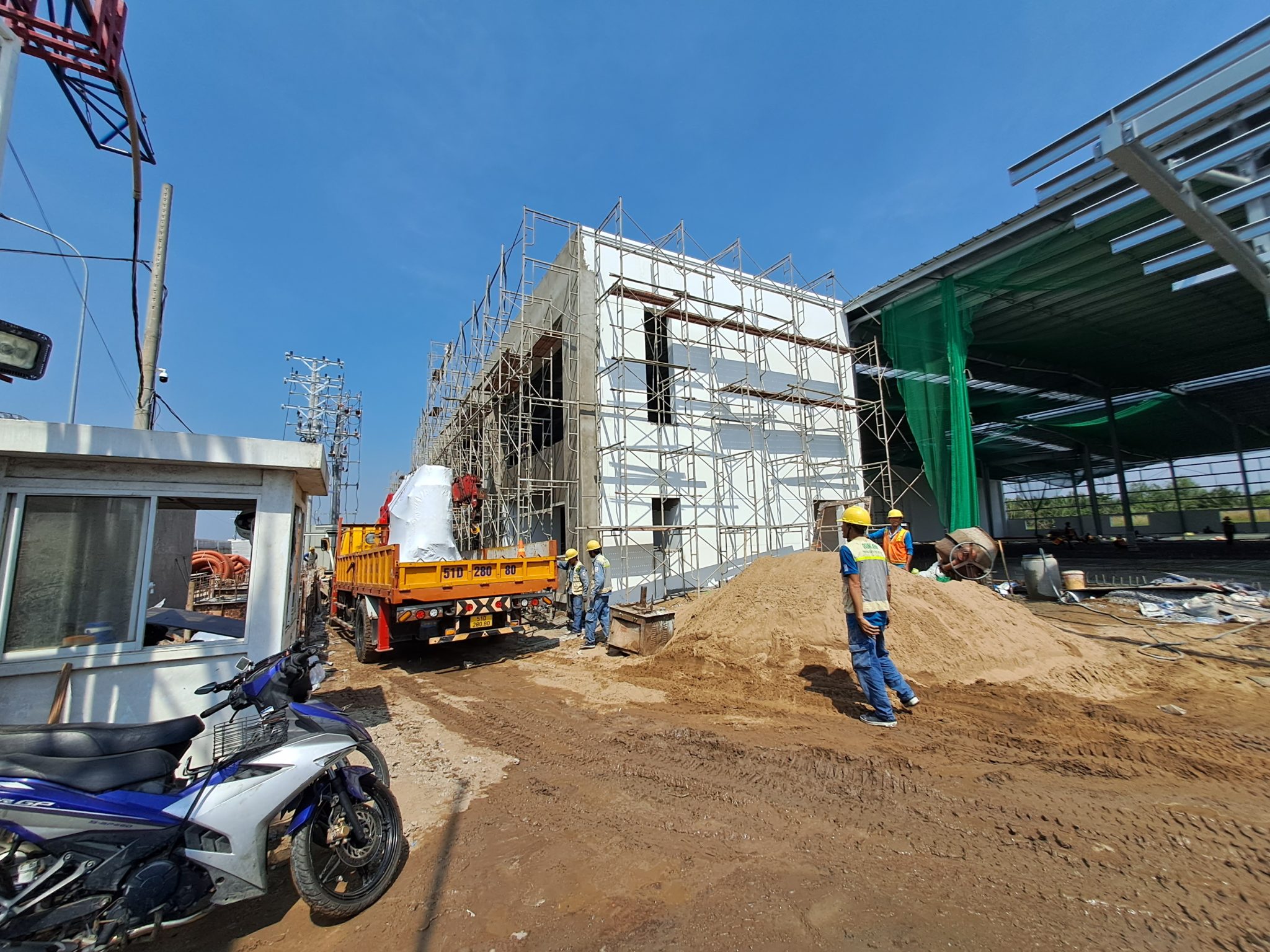
Mandatory Technical Requirements in System Design
Industrial electrical system design must meet stringent technical requirements, including safety factors such as insulation and fire resistance during installation and operation. Load balancing is also crucial for the system to run smoothly, avoiding overload. Accurate electricity consumption costing with low error rates and compliance with TCVN electrical industry standards are essential.
System design requires not only precise technical aspects but also compliance with standards for high performance, safety, and sustainability. Below are fundamental technical requirements to consider during the design process:
HVAC System Design Requirements
- Design standards: Engineers need to adhere to TCVN 5687-2010 standards for air conditioning and ventilation systems, along with SMACNA standards for ductwork fabrication.
- Air quality: Ensure indoor air quality by maintaining fresh air supply standards from ASHRAE.
Technical System Design Requirements in Hospitals
- Wastewater treatment: Wastewater treatment systems must comply with TCVN 7382:2004 and TCVN 6772:2000 standards to ensure the quality of water discharged into the environment.
- Safety and hygiene: A safe and hygienic environment must be guaranteed for both patients and staff.
Safety Requirements in M&E System Design
- Compatibility: Ensure the compatibility of products and M&E systems to facilitate international trade and effective use.
- Safety standards: Comply with international and national safety standards to avoid accidents and ensure smooth system operation.
Fire Protection System Design Requirements
- Instant fire alarms: The system must be able to detect fires rapidly and trigger alarms immediately to ensure safety during evacuations.
- Signal anti-interference capability: Designing the fire alarm system independent of other building systems is very important.
Work System Design Requirements
< ul>
These requirements underscore the importance of adhering to design standards to achieve electrical load balancing, ensuring safety and optimizing electricity cost estimation.
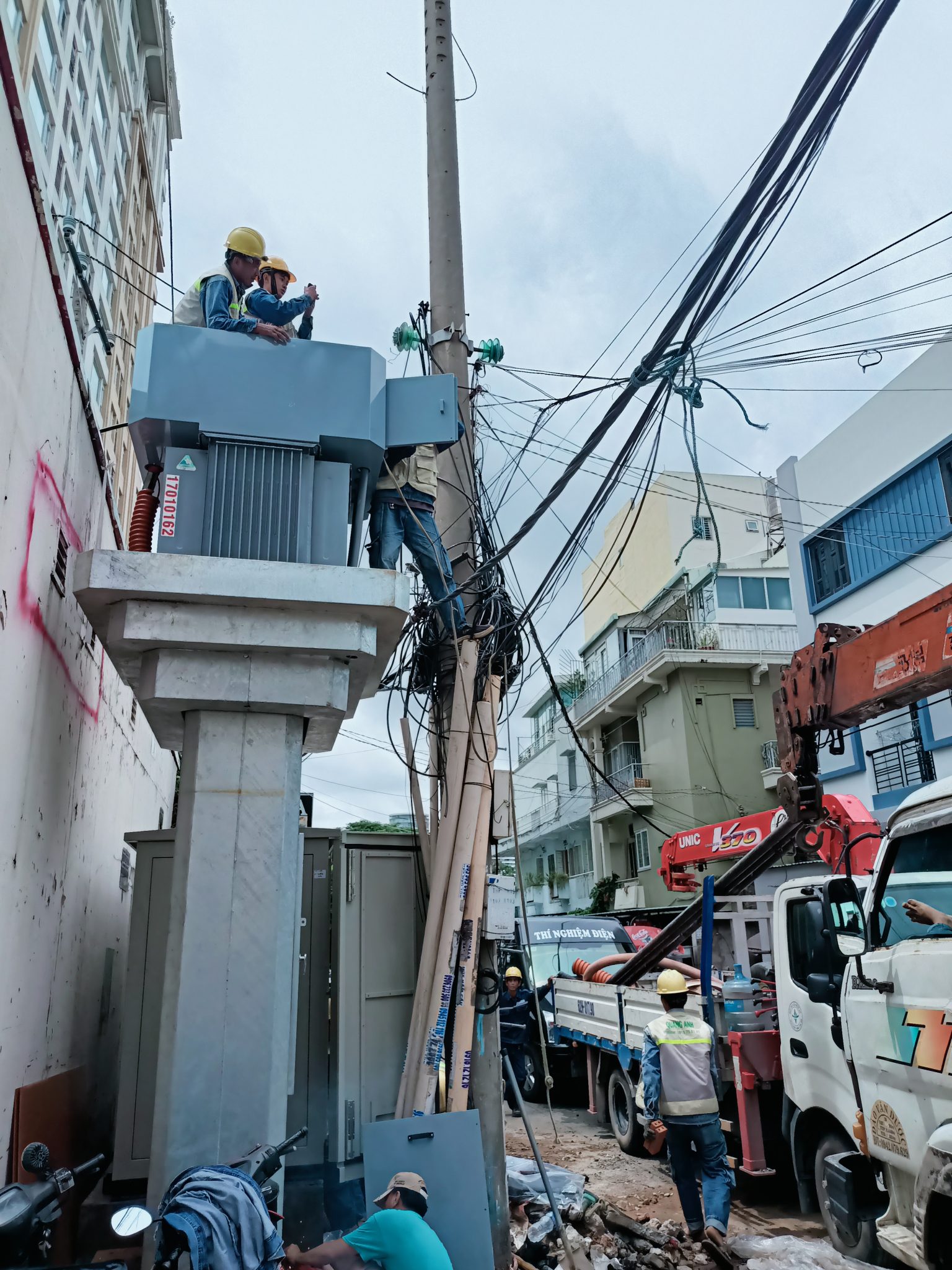
Trends in Industrial Electrical System Applications
Currently, smart electrical monitoring systems are an emerging trend, integrated with IoT to track real-time electricity consumption. Renewable energy, such as solar panels, is also incorporated to alleviate reliance on traditional grid power, providing economic and environmental benefits.
In the context of global green transition, Vietnam’s industrial electricity sector is rapidly integrating advanced solutions to increase efficiency and preserve the environment.
Notably, there is a strong shift towards renewable energy like solar and wind power, marking the commitment of the industrial electricity sector to minimizing negative environmental impacts. This helps establish a sustainable energy ecosystem while creating new economic opportunities by optimizing operational costs and improving energy efficiency.
Simultaneously, intelligent industrial electricity is advancing rapidly. This system improves energy control and management, enabling businesses to optimize electricity usage and reduce greenhouse gas emissions. This solution is necessary for the demands of sustainable manufacturing in the near future.
The role of electrical automation in industrial plants is also becoming increasingly important. Integrating automation systems enhances labor productivity, reduces production costs, and improves output product quality. This aligns with the development trend of modern smart factories.
Additionally, the smart energy network is changing how energy is produced and consumed. Industrial electrical devices like generators are being deeply integrated into this network, thereby not only optimizing distribution but also minimizing energy waste and strengthening system stability.
Lastly, the development of modern industrial electrical devices is vigorously promoted. New devices from ABB, Mitsubishi, Eaton, and Schneider Electric enhance performance, speed up processing, and save costs, meeting the ever-evolving market demands of the industrial electricity sector.
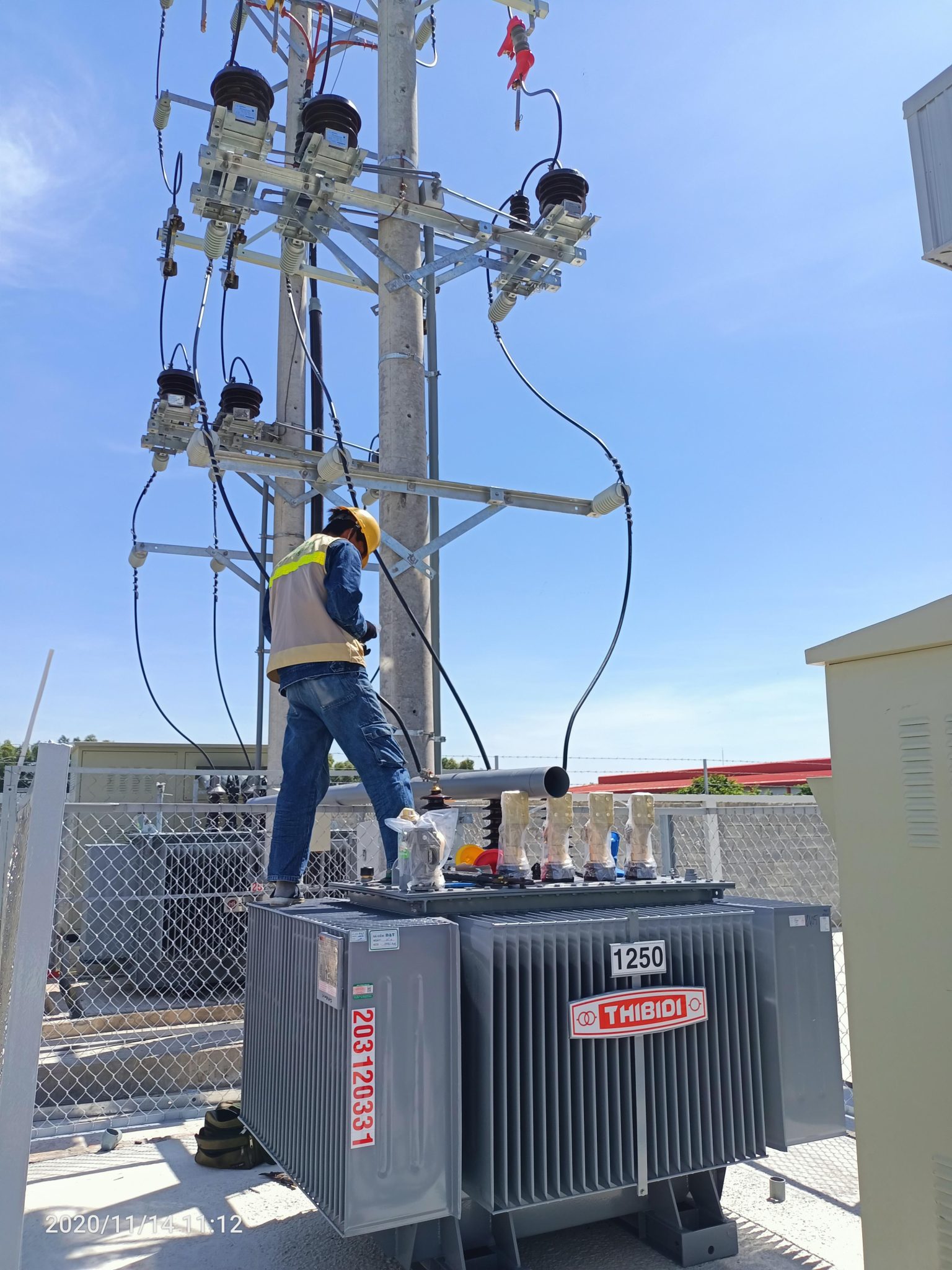
Effective industrial electrical system design not only ensures operational safety but also optimizes costs and increases equipment durability. The application of new technologies such as IoT and renewable energy helps businesses achieve sustainability goals and save energy.
Explore optimal industrial electrical system design solutions with QuangAnhcons. Contact via Hotline: +84 9 1975 8191 for detailed consultation.
QuangAnhcons provides industrial electrical system design and installation services with high safety and efficiency standards, applying advanced technology to ensure sustainable system operation.