Factory electrical system maintenance is an essential activity that ensures the continuity, safety, and efficiency of production equipment.
Detailed Electrical System Maintenance Process
The factory electrical system maintenance process requires periodic checks of the system’s overall condition to detect signs of faults or malfunctions. Measuring voltage and current of each phase in the electrical panel and comparing with previous parameters is an important step in the process. Cleaning and servicing equipment by removing dust and grease buildup ensures smooth operation and avoids electrical short circuits. Replacing defective parts and adjusting equipment to operate correctly is necessary. Ensuring electrical safety standards are maintained for all equipment. Careful documentation and reporting of maintenance activities, inspection results, and problem-solving methods is the final but critically important step.
- Preparation and Load Disconnection
- Disconnect power as needed to ensure safety for maintenance personnel. This includes cutting the load from the generator and disconnecting the main fuse of the control cabinet.
- Thoroughly prepare the necessary tools and equipment.
- Operational Parameter Recording
- Record the operational log from the customer.
- Note down the input and output voltage values of the system.
- Conduct Maintenance
- Periodic Check: Inspect the overall condition of the electrical system to detect signs of faults, malfunctions, leakage currents, and wear.
- Equipment Cleaning: Remove dust and grease build-up on electrical equipment, ensuring electrical system safety.
- Maintenance and Replacement: Maintain parts to ensure smooth operation and replace defective components.
- Safety Check
- Ensure that all equipment and systems comply with safety standards.
- Conduct necessary tests to confirm the electrical system’s safety.
- Inspection and Testing
- After completing the maintenance, conduct inspections and tests on the system to ensure stable and efficient operations.
- Report Results
- Create a detailed report on maintenance results, including identified issues and actions taken. This is an important step in the maintenance system reporting process.
- Propose improvements for the next maintenance process.
- Training and Upgrading
- Ensure maintenance staff are fully trained in technical skills and safety.
- Keep staff continuously updated with skills.
During periodic electrical maintenance, technicians should strictly adhere to safety regulations and use personal protective equipment to ensure safety for both staff and the electrical system. This detailed electrical system maintenance process not only helps the system operate better but also prevents unwanted incidents.
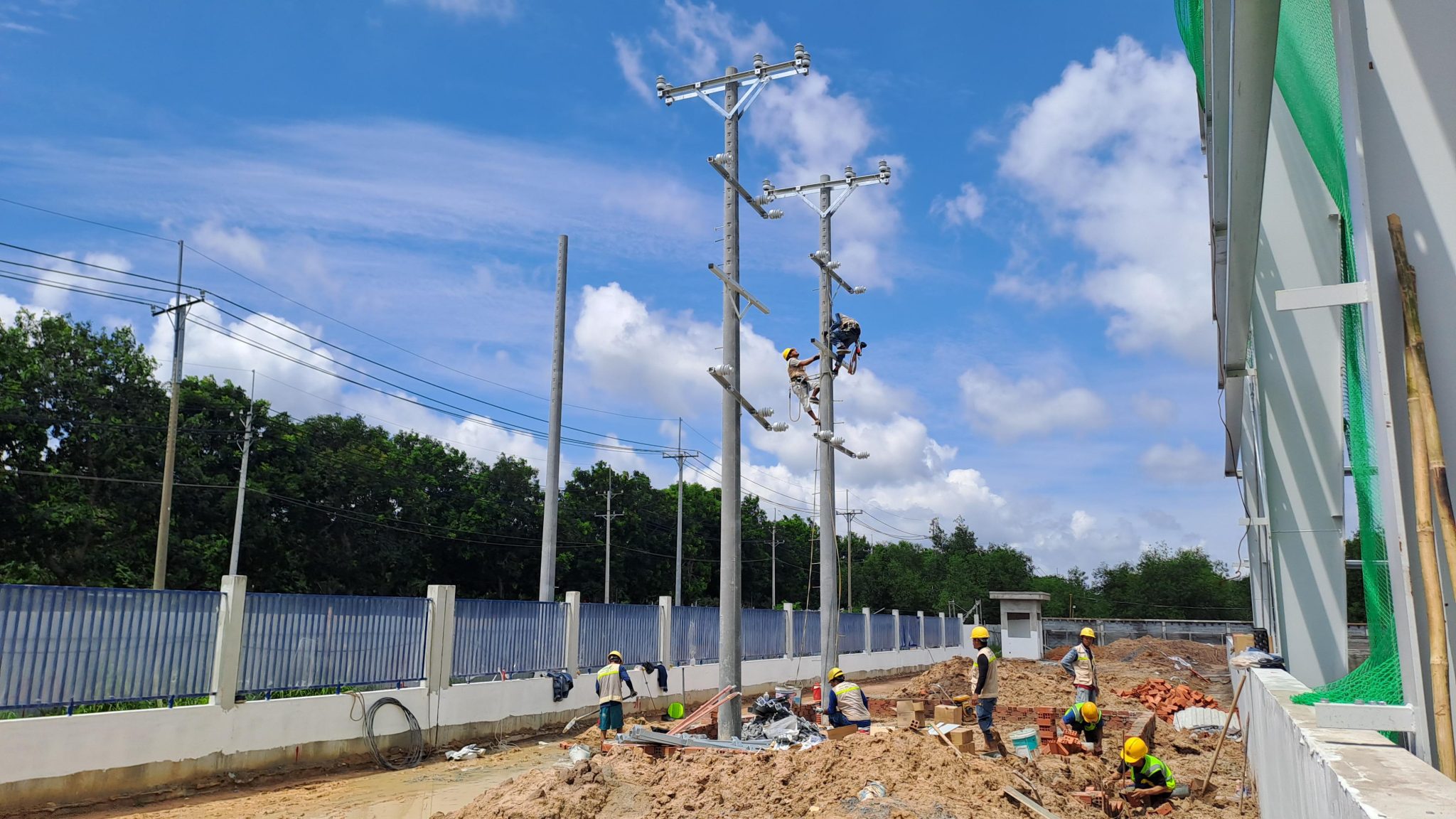
Notes on Electrical System Maintenance
In factory electrical system maintenance, anticipate potential problems to have timely repair solutions. Preparing emergency supplies and machinery is essential. Building plans for system upgrades or conversions to meet new requirements and improve performance should also be prioritized. Adequate staff training on techniques and factory electrical safety ensures effective and safe operations.
Electrical system maintenance is indispensable to ensure effective factory operations. For proper maintenance, engineers need to execute the important steps below.
Assessing Fault Causes and Preparing Techniques
- Before maintenance, determining the source of the problem is very necessary. This includes checking for leakage current, short circuits, or overload conditions.
- Fully disconnect electricity in the maintenance area to avoid risks, and isolate staff from that area.
- Use protective equipment such as insulated gloves, safety shoes, and measurement equipment to ensure safety.
Electrical System Inspection
- Monitor and assess temperature and vibration of equipment to detect overheating and damage phenomena.
- Thoroughly inspect wiring and connections to avoid phenomena such as oxidation, looseness, or disconnections.
- Use measuring devices to check insulation resistance and identify leakage currents to ensure technical safety.
Cleaning and Maintenance
- Remove contaminants such as dust and grease on equipment to prevent fire hazards.
- Lubricate mechanical parts such as CBs, contactors to reduce friction and extend lifespan.
- Inspect the surrounding environment including humidity and temperature to avoid affecting equipment efficiency.
Replacement and Upgrading
- Priority replacement of damaged components with IEC or TCVN standard products to ensure safety and efficiency.
- Record detailed faults detected along with solutions to optimize maintenance schedules for the future.
- Update existing monitoring software to enhance accuracy in fault detection and handling.
Safety and Compliance
- Strictly adhere to regulations on safe distances when working with high voltage electricity.
- Before operation, conduct no-load testing to ensure safety.
- Thoroughly and regularly train staff on new techniques and how to handle emergencies.
Special Notes
- Avoid using homemade devices to minimize risks during repairs.
- Ensure backup systems are arranged so that critical equipment can operate without interruption.
- Conduct lightning protection and grounding system checks at least every 6 months to maintain effectiveness.
Maintaining these systems requires high skill and thorough preparation not only to prevent potential failures but also to ensure smooth operation and cost savings.
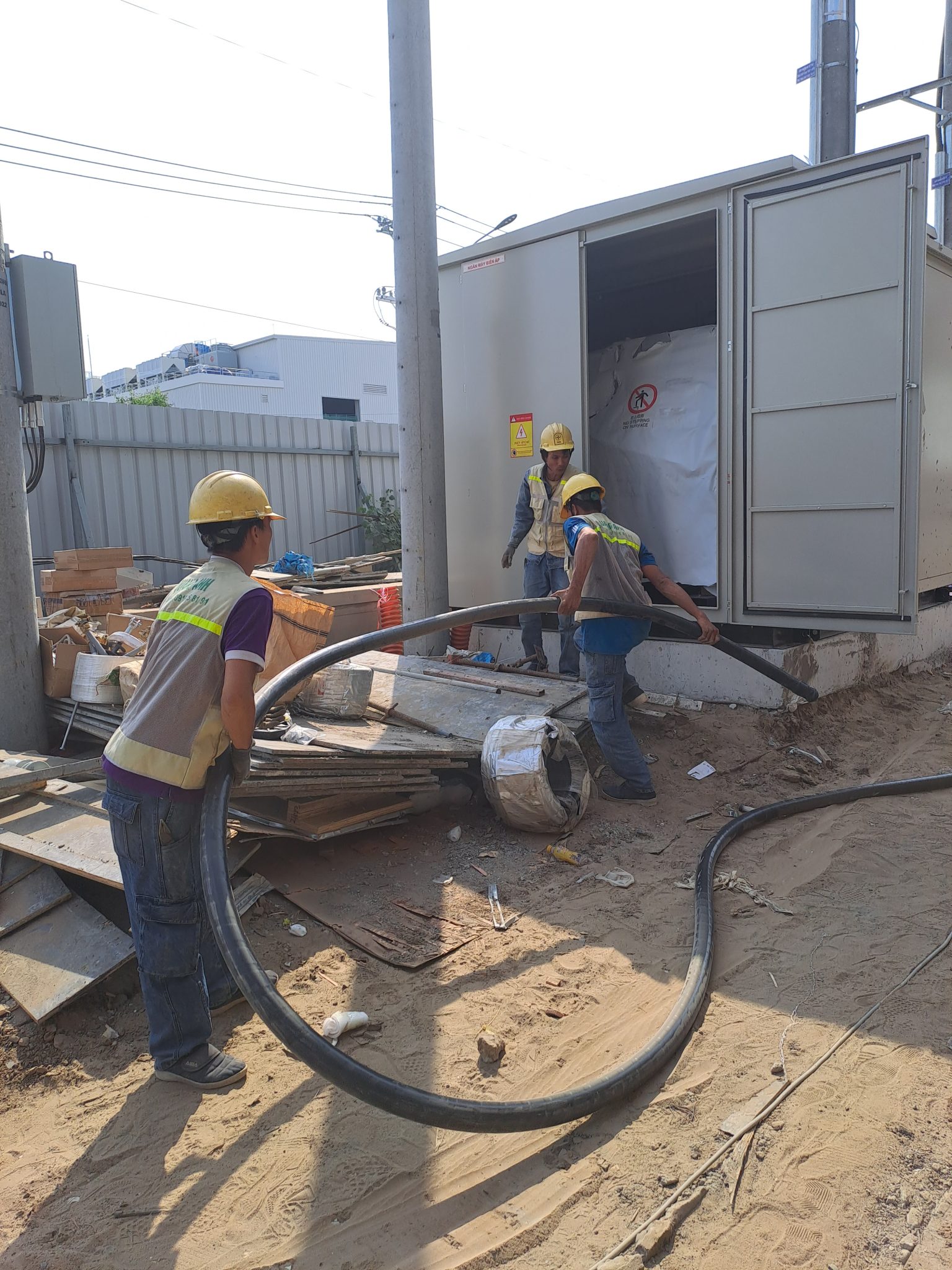
Challenges and Opportunities in Electrical System Maintenance
Maintaining the factory electrical system not only optimizes efficiency and minimizes downtime but also ensures operator safety and saves long-term costs. This is an opportunity for new technology applications, enhancing efficiency and improving all aspects of the electrical system.
In the context of modern industry, electrical system maintenance plays a key role in ensuring electrical system safety and optimizing electrical efficiency. However, challenges abound and require special attention from businesses.
Challenges
- Technology Compatibility: A major challenge is ensuring that equipment and software in new technology systems are compatible with each other. Unresolved compatibility issues can lead to disruption in electrical monitoring and electrical maintenance.
- Continuous Technology Change: Rapid technological development requires continuous updates in knowledge and skills, necessitating significant investment in training by businesses.
- Labor Costs and Incidents: High labor costs and the risk of unplanned incidents can significantly increase total electrical system maintenance costs.
- Environment and Safety: Ineffective maintenance can pose occupational safety risks and negatively impact the environment, especially increasing carbon emissions when maintenance activities are delayed.
Opportunities
- Increase Productivity and Cost Savings: Applying new maintenance technologies helps quickly detect and solve problems, thereby saving maintenance costs and minimizing downtime.
- Enhanced Safety: Modern electrical monitoring methods offer safer procedures, minimizing workplace accident risks.
- Predict and Reduce Incidents: Advanced maintenance technology allows for incident prediction and prevention through data analysis, ensuring continuity for electrical operations.
- Resource Optimization: Modern maintenance systems have the capability to optimize resources, reduce waste, and enhance overall efficiency.
In conclusion, while maintaining the electrical system presents many challenges, employing new technology solutions opens significant opportunities for businesses to improve electrical efficiency and safety.
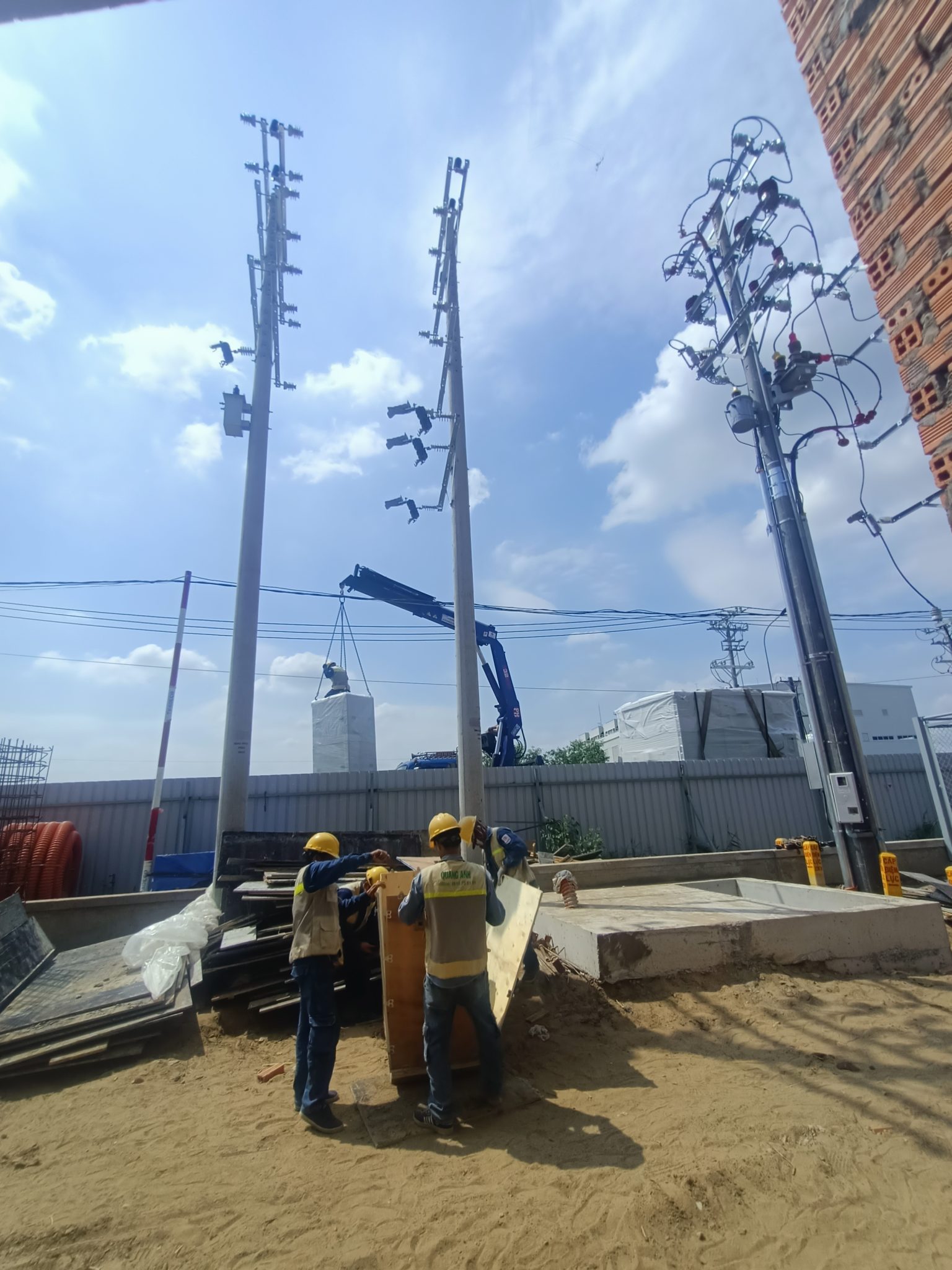
Application of New Technology and the Future of Factory Electrical Systems
The application of new technologies like IoT in monitoring and analyzing the performance of factory electrical systems helps improve the maintenance process. It’s time to consider transitioning to renewable energy sources to reduce environmental impact and long-term costs.
New technology applications are central to the transformation of factory electrical systems. With the advent of flexible solutions, there is an opportunity to optimize both cost and environmental efficiency.
Flexible Electrical Technology
According to research from Wärtsilä (2024), applying flexible power plants in integrated renewable energy systems could save up to €65 trillion by 2050. These plants allow for rapid capacity adjustment to stabilize the grid, reducing the need for new renewable energy installations by half and occupying less space.
An important electric technology solution is the real-time coordination system, where high-speed control technologies ensure renewable energy equipment like solar panels is synchronized with storage systems (BESS) to maintain stable current/voltage.
Virtual Power Plant and the Smart Grid
Virtual Power Plant (VPP) integrates multiple distributed sources like rooftop solar energy, storage battery systems, and controllable loads to optimize supply-demand balance. VPP allows for fast-response services through controlling electric vehicle charging times or supplying reserve power at peak demand. This system also uses historical data to forecast renewable energy output and optimize energy sources in real-time.
Industry 4.0 in Operational Management
IoT and automatic monitoring systems provide superior connectivity and data analysis capabilities in electrical systems. IoT sensors collect voltage and load current parameters, transmitting them to the control center for analysis using big data analytics. System modeling helps evaluate and plan before actual deployment.
Future Trends
Future trends for electrical systems include the development of microgrids integrated with renewable energy, where local systems are autonomous by combining renewable energy, storage, and backup generators. Additionally, self-healing systems become more feasible with AI and smart breakers, quickly restoring power and automating emergency responses.
The factory electrical system is evolving thanks to:
- Multi-source integration to provide flexibility for power generation,
- Optimization through data with the support of IoT and AI,
- Reduced operational costs thanks to advanced storage technology and smart management models.
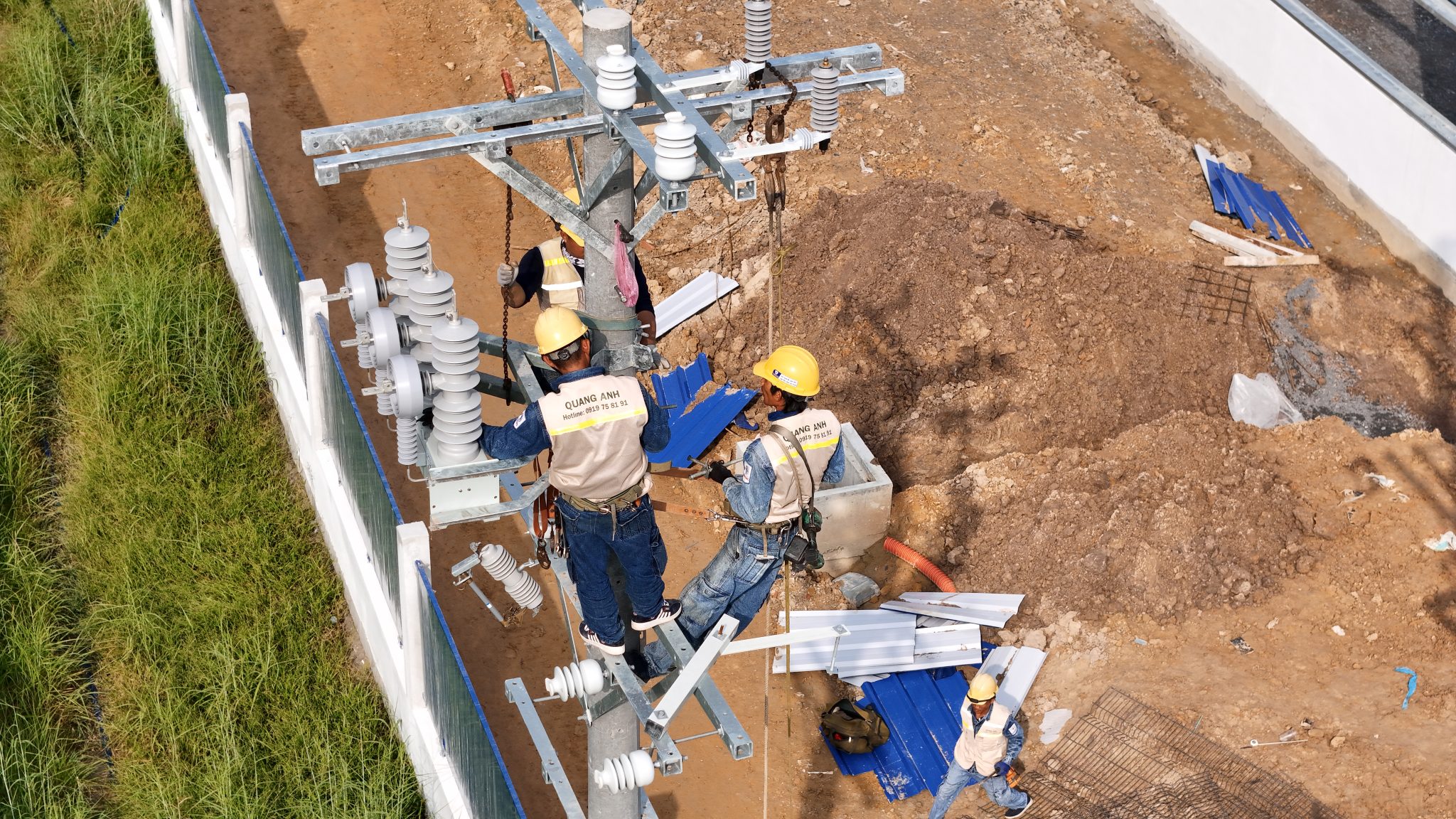
Maintaining the electrical system in the factory not only ensures operational effectiveness but also provides many technical and strategic benefits to businesses. Applying technology and optimizing processes is a solid foundation for sustainable development.
Contact QuangAnhcons today via Hotline: +84 9 1975 8191 for consultation on factory electrical system maintenance solutions.
QuangAnhcons provides factory electrical system maintenance services, ensuring continuous and safe operations while applying advanced technology to enhance efficiency and sustainability.