Electrical System Maintenance in a factory is a crucial process to ensure continuous and safe operations, optimizing production efficiency through preparation, execution, and evaluation.
Preparation Before Conducting Maintenance
Preparing for factory electrical system maintenance includes ensuring occupational safety by equipping full protective gear and isolating the maintenance area. This is to prevent incidents from occurring during electrical system maintenance.
To ensure safe and effective electrical system maintenance, detailed preparation is necessary. Thorough maintenance planning not only optimizes resources but also reduces potential risks. Here are the steps to be followed:
1. Planning
- Risk Assessment: Before conducting electrical system maintenance, the first task is to assess possible risks. This helps craft timely response plans to minimize damage. Choosing appropriate timing, usually during equipment downtime or scheduled maintenance, and effective communication with relevant parties is indispensable.
2. Proposal and Approval
- Detailed Proposal: Develop a detailed proposal including schedule, manpower, and necessary materials. This proposal should be sent to relevant departments like administration at least 3 days before starting for sufficient time for approval and preparation.
3. Preparing Tools and Materials
- Tool Gathering: Ensure readiness of maintenance tools. Check the condition of equipment and tools to secure safety before the maintenance process.
4. Ensuring Workplace Safety
- Security and Hygiene: Ensure the area is safe, prevent unauthorized access and maintain ventilation to prevent toxic substances. Setting safe paths for workers provides ideal working conditions.
5. Equipment Shutdown
- Shut Down and Disconnect: Shutting down equipment and disconnecting power is crucial to ensure safety and avoid accidents.
6. Determining Maintenance Schedule
- Based on Specifications: The maintenance schedule should be based on technical specifications and practical experience. Calculate time and frequency for maintenance for optimal system efficiency.
Detailed preparation before conducting electrical system maintenance not only optimizes the working process but also ensures occupational safety. The key to success is careful planning and thorough execution of each step.
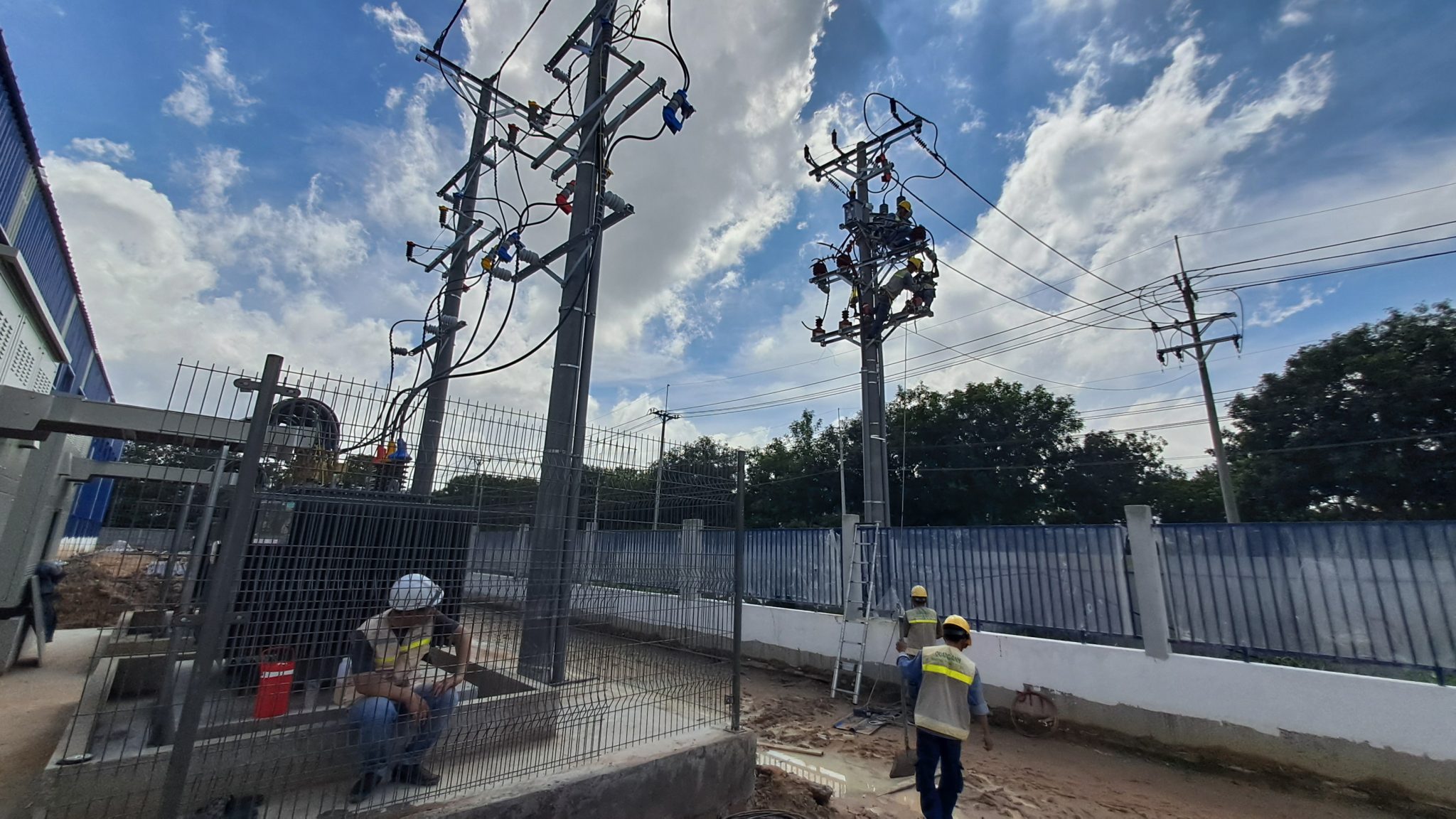
Conducting Maintenance: Necessary Steps
Conducting factory electrical system maintenance not only involves electrical technical inspections but also handling electrical equipment cleaning. Main steps include insulation resistance testing, continuity checks, and dry transformer tests, removing dirt and grease buildup.
Periodic maintenance is essential for optimal electrical system operation. This maintenance process is conducted in specific steps to ensure quality and safety. Below are necessary steps for electrical system maintenance:
- Planning: Firstly, define clear goals and maintenance scope to focus on critical aspects of the electrical system. Collect equipment history, current status, and technical requirements to identify focal points.
- Proposal Creation: Next, create a maintenance proposal with a standardized form, including an implementation plan for an overall project view. Proposals must be sent to administration at least 3 days prior for review.
- Information Verification and Approval: Once a proposal is received, the administration reviews and approves based on information reliability. This process should not exceed 3 working days.
- Preparation for Maintenance: The next task is preparing dossiers, documents, and liaising with suppliers for maintenance. This phase is crucial for personnel and material readiness.
- Conducting Maintenance and Servicing: Perform approved activities related to maintenance and servicing. Ensure the schedule is followed to avoid system operation disruptions.
- Inspection and Evaluation: Finally, once work is completed, inspect and evaluate maintenance results. This includes resistance checks, continuity checks, and transformer inspections to ensure stability. Provide recommendations for future maintenance.
This thorough process not only prevents arising issues but also maintains optimal system performance.
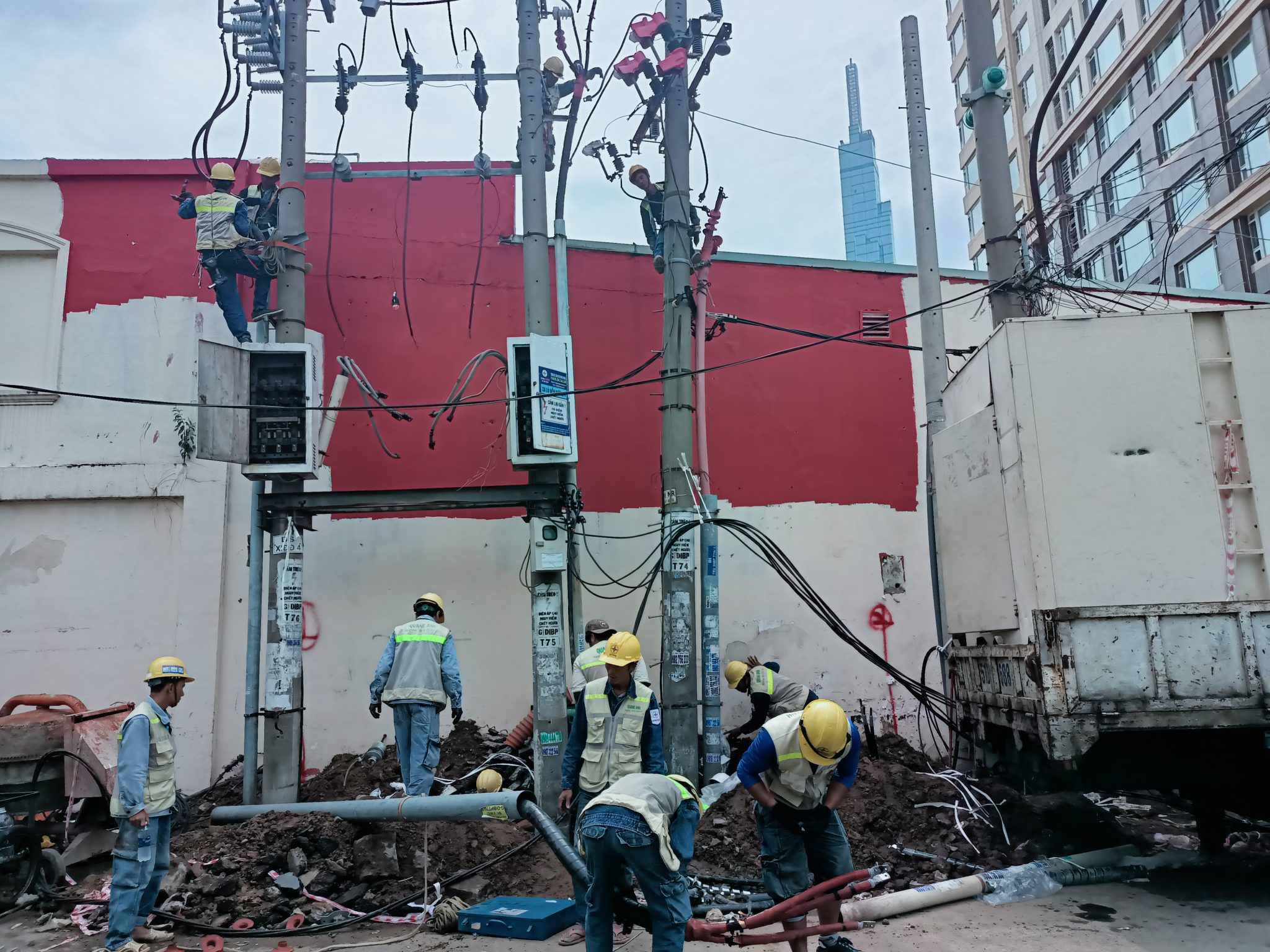
Documentation, Reporting, and Process Improvement
Documenting factory electrical system maintenance activities records issues and actions taken, later analyzing root causes for process improvement.
In the context of modernizing and automating the electrical industry, documenting, reporting, and improving processes are vital for continuous and optimal system operation. Proper templates and processes are necessary to drive this process.
Standard Documentation Templates
Maintaining standard report templates
according to Decision 2429 aids in activity tracking and improvement direction. Notably:
- Improvement Activity Tracking Book: Implementing units need to clearly record goals and performance time for trial evaluations.
- Improvement Proposal Form: A useful tool for analyzing current issues and suggesting necessary organizational changes.
Improvement Reporting Process
A professional improvement process
must follow 7 reporting steps from purpose identification to report completion. Thorough research and data analysis with charts like Pareto ensure feasible and measurable solution proposals.
Improvement Methodology
Utilizing the PDCA tool
is fundamental for continuous improvement (CIP). The PDCA process includes Plan, Do, Check, and Act steps for continuous activity improvement through trials and assessments. Detailed recording is required.
Support Tools
Tools like Ishikawa diagrams and digital documentation
enhance accuracy and efficiency in root cause analysis. Additionally, integrated surveillance checklists in dossiers facilitate process compliance tracking.
Implementation Recommendations
To ensure efficiency when applying new processes, internal training courses on digital documentation
are necessary, along with establishing KPIs to measure form quality and completion speed.
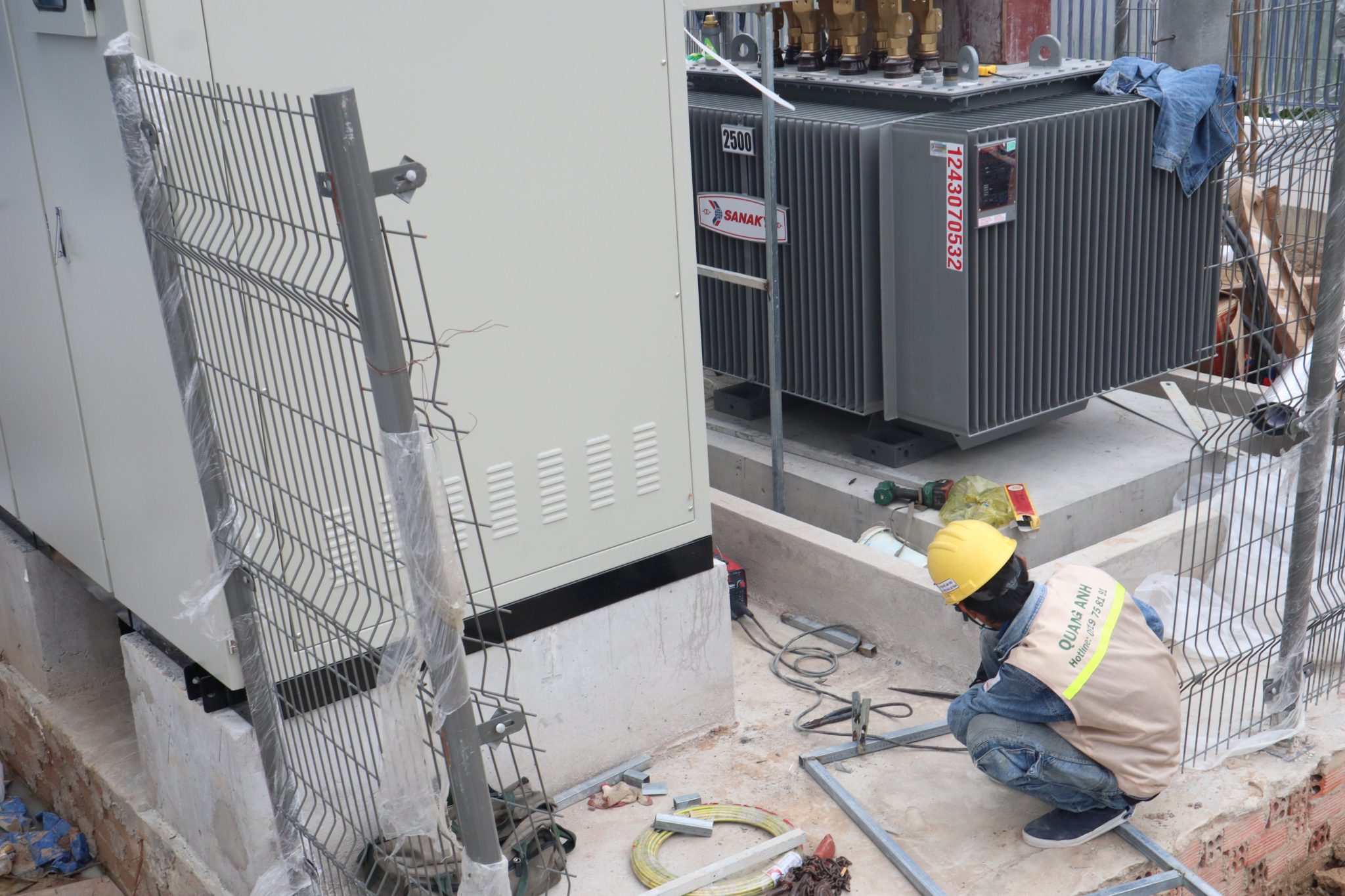
Complying with factory electrical system maintenance processes not only ensures operational efficiency but also is a smart investment strategy, protecting assets and enhancing production safety. Continuous data-driven improvements optimize performance and extend system life.
For enhanced efficiency and safety in factory electrical systems, contact QuangAnhcons via Hotline: +84 9 1975 8191 for consultation and support.
QuangAnhcons specializes in comprehensive factory electrical system maintenance services, ensuring the highest safety and efficiency for customer production operations.