The factory electrical system is an essential part of the infrastructure in industrial plants, ensuring stable and safe electricity supply for production activities.
Main components in the industrial plant electrical system
The factory electrical system includes key components such as transformer station, medium and low voltage cabinets, generators, and switchgear. The transformer station helps convert power from high-capacity lines to levels suitable for use. Medium and low voltage cabinets divide power into separate circuits for each area. Generators are backup devices ensuring the plant operates normally during incidents. Switchgear protects the system from disruptions when the power fluctuates.
The electrical system of an industrial plant requires a complex structure to ensure stable and safe electricity supply. Below is a detailed analysis of each important component within this system, helping business leaders and system engineers gain a more comprehensive and in-depth understanding.
1. Transformer stations, medium voltage and low voltage cabinets
- Transformer stations play a key role in drawing electricity from high-capacity lines and converting it into suitable voltages for plant operations. Ensuring stable voltage helps devices and machinery operate efficiently.
- Medium voltage and low voltage cabinets are important in splitting power sources into smaller electric circuits. Medium voltage cabinets are responsible for distributing power at medium voltage levels, while low voltage cabinets ensure low voltage power supply to end devices. These cabinets help protect and optimize the flow of electricity to each area in the plant.
2. Generator Systems and Switchgear
- Generators act as backup power sources, important in maintaining plant operations when there is an outage from the main power grid.
- Switchgear is an essential device that ensures smooth transition between the grid power and generator. This helps avoid production disruptions caused by power loss or unstable voltage.
3. Distribution Board Systems
- Distribution boards are responsible for installing and protecting switchgear and controlling the flow of electricity within the plant.
- They also ensure safety for workers and the system through functions that isolate electrical equipment from the users.
4. Machinery Control Cabinet Systems
- This group of electrical cabinets is used to control and operate machinery in the plant, playing a decisive role in organizing fully or semi-automatic production operations.
5. Other support systems
- Light electrical systems serve control devices, communication, office equipment, and security.
- Lighting systems ensure safe and efficient working conditions in the plant and surrounding areas.
Most electrical systems in industrial plants use 3-phase power with a voltage of 380V, meeting the large capacity needs for power-driven and control devices.
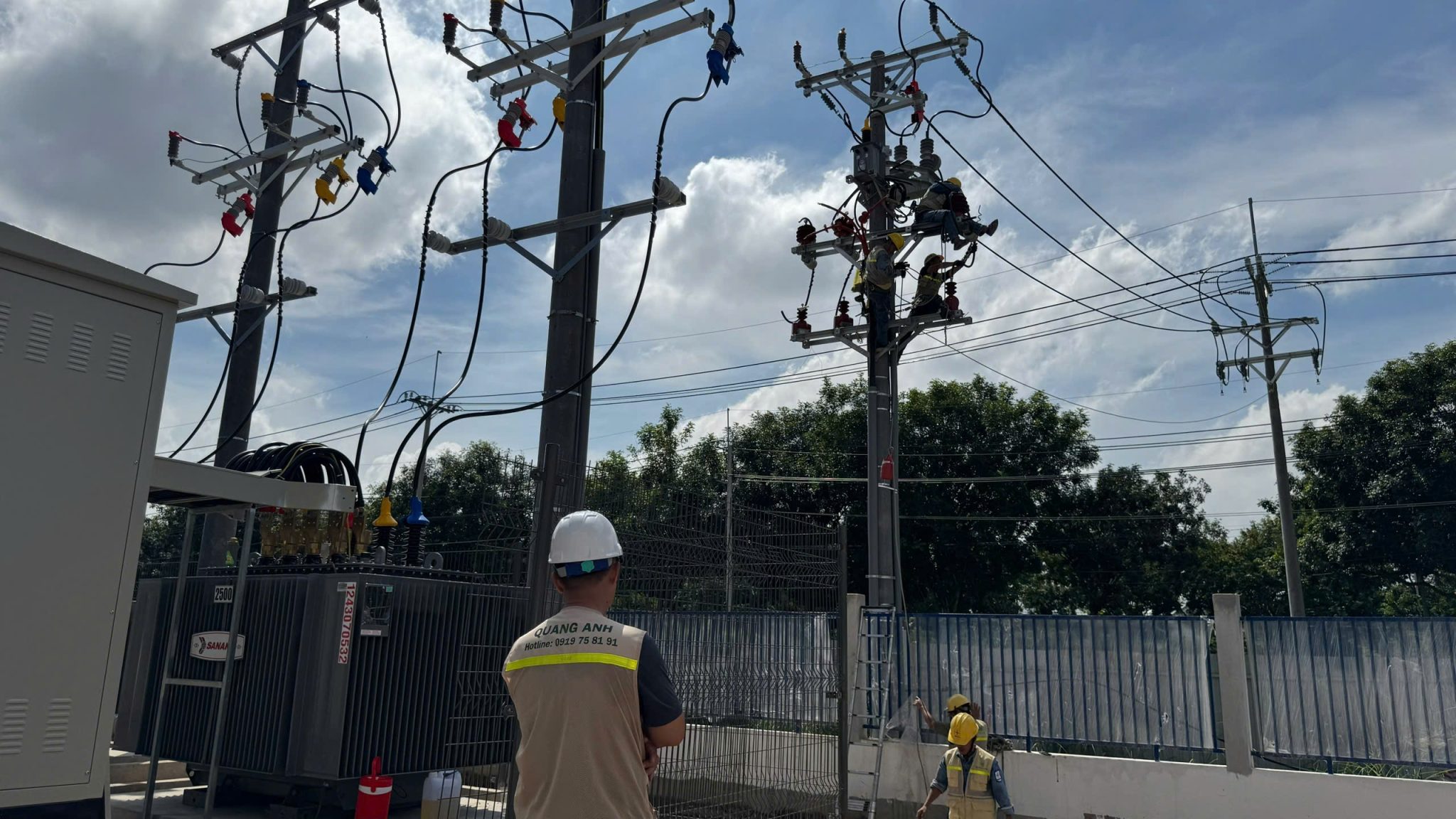
Functions of the Electrical System
The factory electrical system provides energy for equipment and machinery to operate; ensures their precise control; and safeguards user and device safety. Especially, electrical safety plays a crucial role in isolating electricity from users, minimizing occupational hazard risks.
The electrical system plays an indispensable role in ensuring stable and safe electrical energy supply for economic and production activities. Below are the main functions of the electrical system:
1. Supply and Transform Energy
- Supply Electrical Energy: The electrical system is responsible for generating and supplying electricity from sources such as hydropower, thermal power, solar power, wind power, and nuclear power throughout the country.
- Transform Voltage: Using substations from ABB and Schneider to convert voltage from production to distribution levels and finally to usage levels, ensuring suitable voltage for devices and electrical systems.
2. Transmission and Distribution
- Power Transmission: The national grid transports electricity from production sources to usage locations, through high voltage and ultra-high voltage lines, maintaining stable operation.
- Electrical Power Distribution: The electrical system ensures power distribution to every region across the country, effectively meeting the needs of households, businesses, and production facilities.
3. Management and Control
- Load Management: The system needs to be flexible to handle varying consumption intensity over time, ensuring adequate supply when demand is high.
- System Control: Management and control centers ensure the efficient operation of the power network, including monitoring, operating, and maintaining the grid.
4. Ensure Safety and Quality
- Ensure Safety: The electrical system must be absolutely safe, preventing accidents from short-circuits, lightning, or environmental factors.
- Electrical Energy Quality: Ensures stable power supply quality for production, economic development, and daily life.
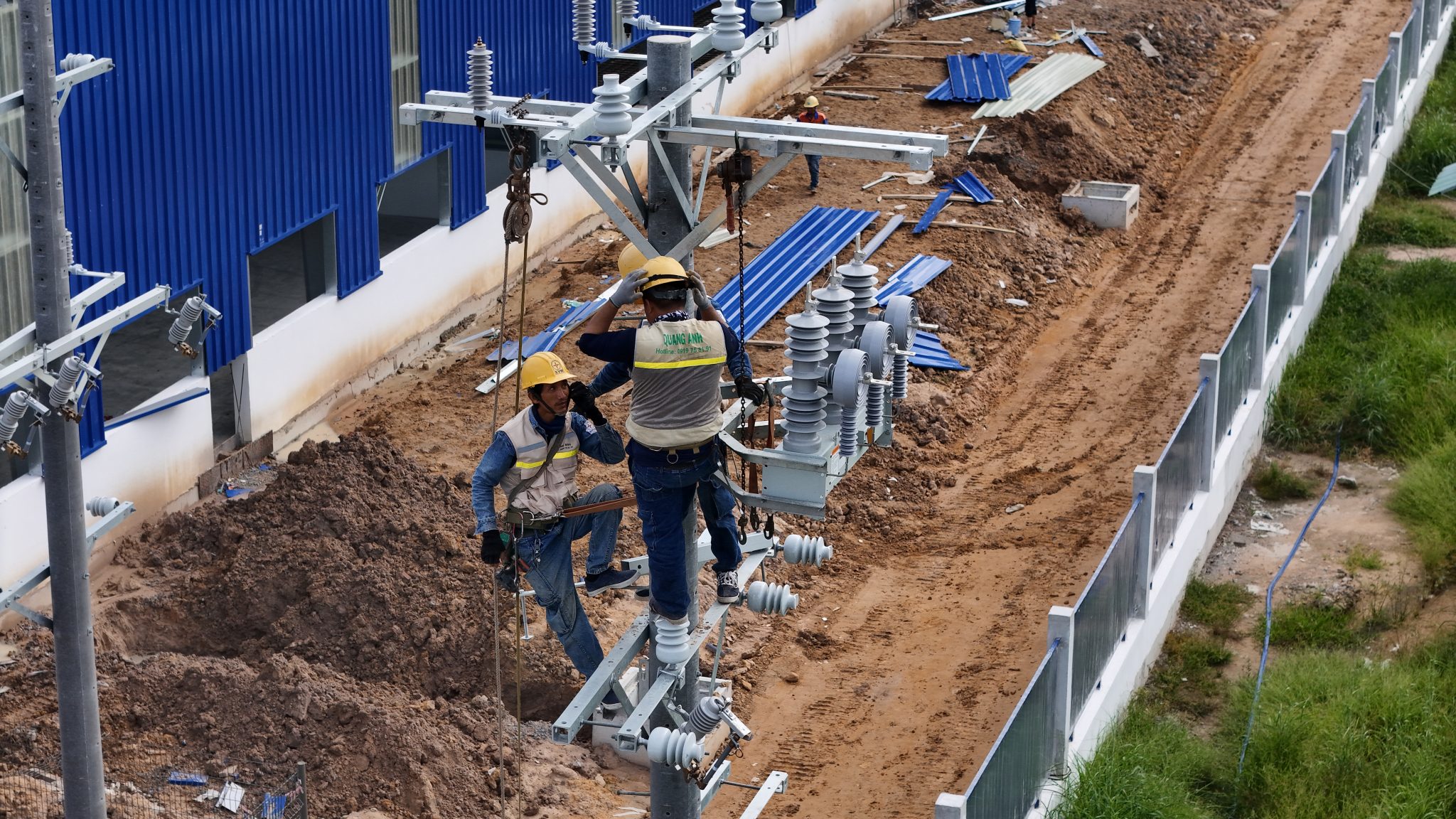
Notes on installing and maintaining the factory electrical system
Installing the factory electrical system requires compliance with national electrical safety standards. Using quality equipment and performing regular maintenance is necessary to ensure the system operates stably and extends equipment lifespan. Care in these steps ensures the system meets continuous and safe production demands.
Installing and maintaining the electrical system in the plant requires attention to many factors to ensure both electrical operation efficiency and minimize industrial safety risks. Safety is always a top priority during installation, protecting not only workers but also machinery in harsh production environments.
To optimize construction progress, adhering to electrical maintenance procedures and nationally regulated electrical design standards is indispensable. Operating the electrical system stably and continuously without interruption is the way to achieve optimal efficiency, reducing energy waste in production.
Detailed design must ensure not only safety but also operational cost optimization, thereby reducing production costs and increasing business competitiveness. Ensure all equipment and materials are ready before execution to avoid shortages causing progress disruptions.
Some essential technical tasks during installation include carefully marking cables and wires to avoid confusion, using safe cable trays with anti-static paint, and calculating capacity for energy consumption optimization. Each step helps reduce electrical energy waste and improve the efficiency of electronic operations.
Periodic maintenance of the system is important to ensure the consistency of the electrical system. Activities such as equipment inspection, system test runs, or load and capacity monitoring help detect potential errors promptly, avoiding severe equipment damage. Keeping detailed maintenance records helps maintain timely periods and upgrade the system as needed to improve overall performance.
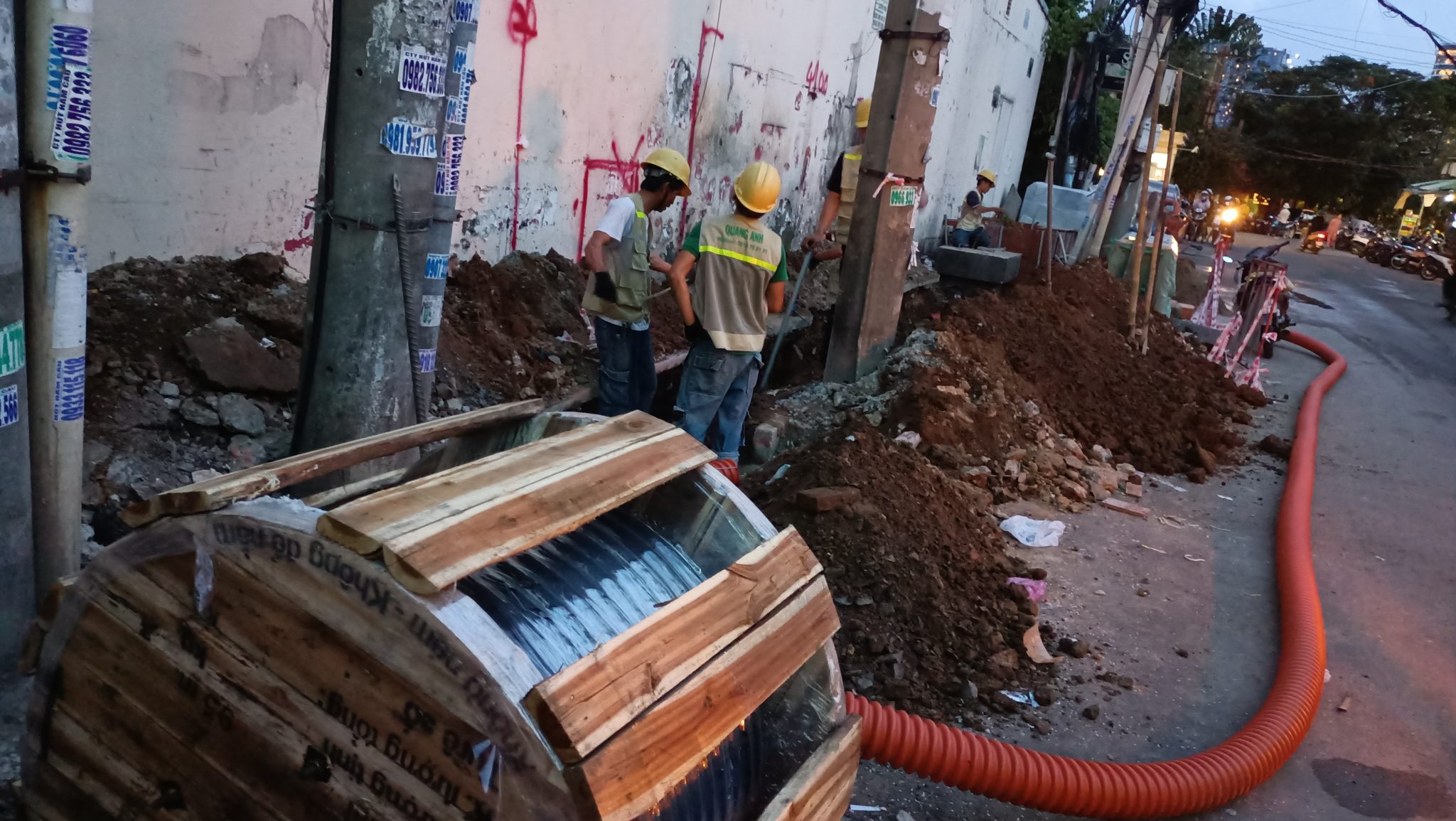
The factory electrical system ensures stability and efficiency for production processes, enhancing occupational safety and maximizing equipment lifespan. Investing in a modern electrical system is a crucial strategic decision for industrial plants.
For consultation on professional design and installation of factory electrical systems, contact QuangAnhcons at hotline: +84 9 1975 8191.
QuangAnhcons provides complete services in the design, installation, and maintenance of electrical systems for industrial plants, ensuring compliance with national standards for electrical safety.